Clamping device and method used for precise machining of outer surface of shape-preserving fairing
A precision machining and clamping device technology, which is applied in positioning devices, metal processing equipment, metal processing machinery parts, etc., can solve the problems of low processing accuracy, improve processing accuracy, reduce local stress concentration, and reduce deformation Effect
- Summary
- Abstract
- Description
- Claims
- Application Information
AI Technical Summary
Problems solved by technology
Method used
Image
Examples
specific Embodiment approach 1
[0016] Specific implementation mode one: as Figure 1~2 As shown, the clamping device for the precision machining of the outer surface of the conformal fairing in this embodiment includes a base 1, a clamping base 3 and several contact units 2, the base 1 is a circular base, and the clamping base 3 is a cylinder shape, one end of the clamping base 3 is fixed on one end surface of the base 1, and on the outer wall of the clamping base 3 there are several contact units 2 arranged in a matrix along its circumferential direction and its axial direction. The outer surfaces are all on the same curved surface, and the curve equation of the curved surface is consistent with the curve equation of the inner surface of the conformal fairing 6, a longitudinal through groove 4-2 is formed between two adjacent rows of contact units 2, and two adjacent rows A transverse channel 4-3 is formed between the contact units 2, and the longitudinal channel 4-2 and the transverse channel 4-3 are inte...
specific Embodiment approach 2
[0017] Specific implementation mode two: as figure 1 As shown, the contour of the contact surface of the contact unit 2 in this embodiment is polygonal or circular. Such a design is used for direct contact with the conformal fairing 6, and the curve equation of the curved surface is consistent with the curve equation of the inner surface of the conformal fairing 6, which reduces the local stress concentration after the conformal fairing 6 is clamped. Other components and connections are the same as those in the first embodiment.
specific Embodiment approach 3
[0018] Specific implementation mode three: as figure 1 As shown, the contact surface profile of the contact unit 2 in this embodiment is rectangular, trapezoidal or triangular. Such a design is used for direct contact with the conformal fairing 6, and the curve equation of the curved surface is consistent with the curve equation of the inner surface of the conformal fairing 6, which reduces the local stress concentration after the conformal fairing 6 is clamped. Other components and connections are the same as those in the second embodiment.
PUM
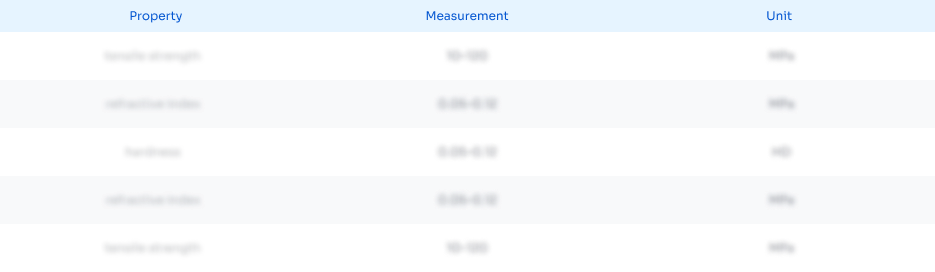
Abstract
Description
Claims
Application Information

- Generate Ideas
- Intellectual Property
- Life Sciences
- Materials
- Tech Scout
- Unparalleled Data Quality
- Higher Quality Content
- 60% Fewer Hallucinations
Browse by: Latest US Patents, China's latest patents, Technical Efficacy Thesaurus, Application Domain, Technology Topic, Popular Technical Reports.
© 2025 PatSnap. All rights reserved.Legal|Privacy policy|Modern Slavery Act Transparency Statement|Sitemap|About US| Contact US: help@patsnap.com