Air-floating type flexible assembly butt-joint system
A flexible assembly, air-floating technology, applied in metal processing, metal processing equipment, manufacturing tools, etc., can solve the problems of poor flexibility, low assembly accuracy, poor efficiency, etc., to ensure flexibility, improve assembly quality, reduce The effect of driving force
- Summary
- Abstract
- Description
- Claims
- Application Information
AI Technical Summary
Problems solved by technology
Method used
Image
Examples
specific Embodiment approach 1
[0039] Specific implementation mode 1: see figure 1 This embodiment will be described. The air-floating flexible assembly docking system described in this embodiment includes an active assembly docking vehicle 1 , a passive assembly docking vehicle 2 and a track 3 ;
[0040] The active assembly docking vehicle 1 and the passive assembly docking vehicle 2 slide along the same track 3,
[0041] The passive assembly docking vehicle 2 is used to lift the passive docking cabin section 4,
[0042] The active assembly docking vehicle 1 is used to lift the active docking cabin section 5, and control the docking movement of the active docking cabin section 5 along the extension direction of the track 3, the movement perpendicular to the extension direction of the rail 3, the vertical movement in the vertical direction, and the yaw rotation , pitch rotation and roll rotation, so as to realize the docking with the passive docking cabin section 4 held on the passive assembly docking vehi...
specific Embodiment approach 2
[0048] Specific implementation two: see figure 2 , Figure 5 and Image 6 Describing this embodiment, the difference between this embodiment and the air-floating flexible assembly docking system described in Embodiment 1 is that the active assembly and docking vehicle 1 includes an air-floating platform rail vehicle 1-1 and a rear air-floating bracket. 1-2. Rear lift bracket 1-3, rear product support ring 1-4, docking guide rail 1-5, front air flotation bracket 1-6, front lift bracket 1-7 and front product support ring 1- 8;
[0049] The air floating platform rail car 1-1 slides along the track 3,
[0050] The upper surface of the air-floating platform rail car 1-1 is the air-floating plane.
[0051] The rear air flotation bracket 1-2 and the front air flotation bracket 1-6 are frictionally connected to the air flotation plane through the air foot 6,
[0052] The docking guide rails 1-5 are fixed on the air-floating platform rail car 1-1. The docking guide rails 1-5 are ...
specific Embodiment approach 3
[0059] Specific implementation mode three: see figure 1 Describing this embodiment, the difference between this embodiment and the air-floating flexible assembly docking system described in Embodiment 1 is that the passive assembly docking vehicle 2 includes a docking rail vehicle 2-1, a support mechanism 2-2 and a limiter Bit institutions 2-3;
[0060] The upper surface of the docking rail car 2-1 is provided with a slideway, the direction of the slideway is parallel to the rail 3, and a number of limit mechanisms 2-3 are arranged on the slideway. The support mechanism 2-2 is connected to the docking railcar 2-1 through the slideway. The upper surface of the support mechanism 2-3 is slidably connected, and the limit mechanism 2-3 is used to limit the limit position of the front and rear sliding of the support mechanism 2-2.
[0061] In this embodiment, after the passive docking cabin section 4 is fixed on the supporting mechanism 2-2 on the docking rail car 2-1, the supporti...
PUM
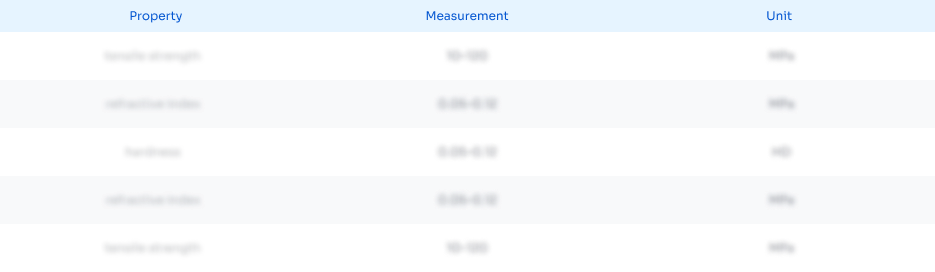
Abstract
Description
Claims
Application Information

- Generate Ideas
- Intellectual Property
- Life Sciences
- Materials
- Tech Scout
- Unparalleled Data Quality
- Higher Quality Content
- 60% Fewer Hallucinations
Browse by: Latest US Patents, China's latest patents, Technical Efficacy Thesaurus, Application Domain, Technology Topic, Popular Technical Reports.
© 2025 PatSnap. All rights reserved.Legal|Privacy policy|Modern Slavery Act Transparency Statement|Sitemap|About US| Contact US: help@patsnap.com