Flexible mechanical arm and control method thereof
A control method and technology of robotic arms, applied in the directions of manipulators, manufacturing tools, chucks, etc., can solve problems such as not being well applicable to a wide range of tasks and environments, low degree of freedom of movement, and inability to change its own shape and size.
- Summary
- Abstract
- Description
- Claims
- Application Information
AI Technical Summary
Problems solved by technology
Method used
Image
Examples
Embodiment Construction
[0030] The present invention will be further described below in conjunction with the accompanying drawings and specific embodiments.
[0031] see figure 1 As shown, a flexible robotic hand of the present invention includes: a hand-shaped body, a drive assembly 3, and a control assembly 2. The fingers of the hand-shaped body include several execution bodies 1, and the execution bodies 1 include elastic cavities. , the elastic cavity is provided with a first fixing member that restricts the radial expansion of the elastic cavity and a second fixing member that restricts the axial expansion of one side of the elastic cavity, and the drive assembly 3 is connected with the elastic cavity and controlled The pressure in the elastic cavity, the control assembly 2 includes a controller for controlling the drive assembly 3, a bending sensor arranged axially along the elastic cavity, an inertial sensor arranged at intervals along the axial direction of the elastic cavity, and one end is ...
PUM
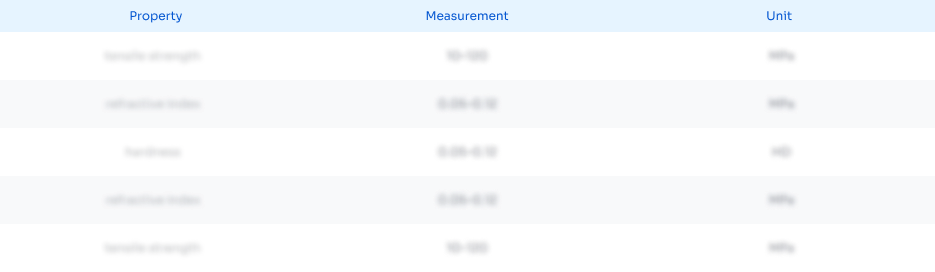
Abstract
Description
Claims
Application Information

- R&D Engineer
- R&D Manager
- IP Professional
- Industry Leading Data Capabilities
- Powerful AI technology
- Patent DNA Extraction
Browse by: Latest US Patents, China's latest patents, Technical Efficacy Thesaurus, Application Domain, Technology Topic, Popular Technical Reports.
© 2024 PatSnap. All rights reserved.Legal|Privacy policy|Modern Slavery Act Transparency Statement|Sitemap|About US| Contact US: help@patsnap.com