Mold for manufacturing turbocharger
A cooling technology for molds and molds, which is applied in the manufacture of tools, casting molding equipment, casting molds, etc., can solve the problems of difficult recovery of cooling water, increase of production costs, slow cooling rate, etc., to avoid flash burrs and air leakage, Improve production efficiency and fast molding effect
- Summary
- Abstract
- Description
- Claims
- Application Information
AI Technical Summary
Problems solved by technology
Method used
Image
Examples
Embodiment Construction
[0020] The present invention will be described in detail below in conjunction with the accompanying drawings.
[0021] Such as figure 1 , figure 2 , image 3 As shown, a kind of turbocharger manufacturing mold of the present invention comprises upper mold 1, lower mold 2, base 3, feed inlet 4, upper mold cooling interlayer 5, upper mold cavity 6, mold core 7, lower mold Cavity 8, lower mold cooling interlayer 9, inserting plate 10, inserting plate groove 11, upper mold fixed side 12, lower mold fixed side 13, fixing screw 14, nut 15, cooling thermostat 16, cooling medium input pipe 17, connecting pipe 18. Cooling medium output pipe 19, first fixing plate 20, first mold core fixing hole 21, upper mold fixing hole 22, lower mold fixing hole 23, second fixing plate 24, second mold core fixing hole 25.
[0022] The base 3 is fixed with a lower mold 2, the lower mold 2 is provided with a mold core 7, the mold core 7 is provided with an upper mold 1, and the upper end of the upp...
PUM
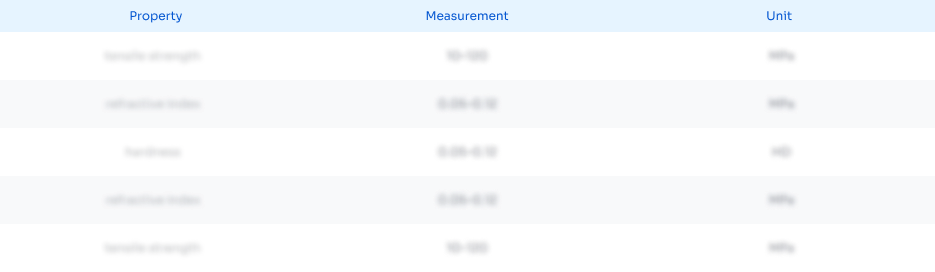
Abstract
Description
Claims
Application Information

- R&D Engineer
- R&D Manager
- IP Professional
- Industry Leading Data Capabilities
- Powerful AI technology
- Patent DNA Extraction
Browse by: Latest US Patents, China's latest patents, Technical Efficacy Thesaurus, Application Domain, Technology Topic, Popular Technical Reports.
© 2024 PatSnap. All rights reserved.Legal|Privacy policy|Modern Slavery Act Transparency Statement|Sitemap|About US| Contact US: help@patsnap.com