A treatment method for waste gas in the production process of viscose fiber
A production process, viscose fiber technology, applied in the treatment of waste gas, the field of waste gas treatment in the production process of viscose fiber, can solve the problem that waste gas cannot be decomposed into harmless gas, etc., to improve the working environment of workers, simple operation, security Effects on Workers' Health
- Summary
- Abstract
- Description
- Claims
- Application Information
AI Technical Summary
Problems solved by technology
Method used
Examples
Embodiment 1
[0029] A treatment method for waste gas in the viscose fiber production process, comprising the following method steps:
[0030] A. Primary alkali spray pretreatment
[0031] Alkali spray towers are connected in series to form a first-stage alkali spray tower. Carbon disulfide and hydrogen sulfide waste gas pass through the first-stage alkali spray tower, and after alkali spray and filler interception, collision and absorption, hydrogen sulfide, a small amount of carbon disulfide and dissolved Volatile organic compounds;
[0032] B. Reaction decomposition
[0033] The exhaust gas pretreated by the first-level spray tower in step A is first dewatered through the buffer tank, and then transported to the low-temperature plasma device through the pipeline to decompose the pollutants in the exhaust gas into small molecular fragments;
[0034] C. Catalytic oxidation
[0035] Transport the waste gas from step B through the low-temperature plasma device to the catalytic oxidation t...
Embodiment 2
[0044] On the basis of embodiment 1:
[0045] Preferably, the wind volume of the exhaust gas is 50,000 m 3 / h, the first-stage alkali spray tower is two alkali spray towers connected in series, and the second-stage alkali spray tower is two alkali spray towers connected in series.
[0046] Preferably, the rated gas volume of the low temperature plasma device is 50,000 m 3 / h, maximum power 50Kw, input voltage 380v.
Embodiment 3
[0048] On the basis of embodiment 1:
[0049] Preferably, the wind volume of the exhaust gas is 100,000 m 3 / h, the first-stage alkali spray tower is 6 alkali spray towers connected in series, and the second-stage alkali spray tower is 6 alkali spray towers connected in series.
[0050] Preferably, the rated gas volume of the low temperature plasma device is 100,000 m 3 / h, maximum power 80Kw, input voltage 380v.
PUM
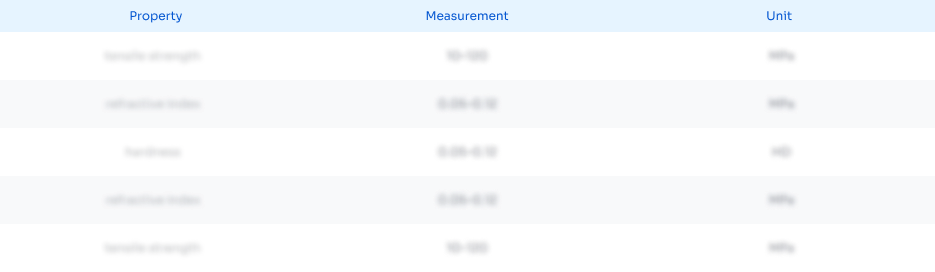
Abstract
Description
Claims
Application Information

- R&D
- Intellectual Property
- Life Sciences
- Materials
- Tech Scout
- Unparalleled Data Quality
- Higher Quality Content
- 60% Fewer Hallucinations
Browse by: Latest US Patents, China's latest patents, Technical Efficacy Thesaurus, Application Domain, Technology Topic, Popular Technical Reports.
© 2025 PatSnap. All rights reserved.Legal|Privacy policy|Modern Slavery Act Transparency Statement|Sitemap|About US| Contact US: help@patsnap.com