Construction method for slowly-bonded hollow prestressing floor slab through large-span ultra-thick cast-in-place post-tensioning method
A technology for bonding prestressed and hollow floor slabs, applied in floors, building components, buildings, etc., can solve the problems of insufficient structural performance of unbonded prestressed tendons, instability and collapse of formwork supports, steel bars, and bottom forms floating up, etc. Good anti-floating effect, reduced concrete consumption and accurate positioning
- Summary
- Abstract
- Description
- Claims
- Application Information
AI Technical Summary
Problems solved by technology
Method used
Image
Examples
Embodiment 1
[0032] figure 1 It is a schematic diagram of the ultra-thick cast-in-place post-tensioned prestressed hollow floor slab of the present invention; figure 2 It is a cross-sectional view of the ultra-thick cast-in-place post-tensioned prestressed hollow floor slab invented by the invention. refer to figure 1 , 2 As shown, at the bottom of the ultra-thick cast-in-place post-tensioned slow bonded prestressed hollow floor slab, a support component is arranged, the support component includes a horizontally arranged steel pipe 12 and a vertical bracket 3, and a bottom form 1 is set above the support component and bottom slab steel bars 2, multiple rows and rows of prefabricated hollow blocks 3 are arranged above the bottom slab steel bars 2, and floor slab steel bars are arranged between the prefabricated hollow blocks. 1 side formwork 16 is erected around, the main reinforcement 14 of the floor slab passes through the sideform 16 for easy fixing, and the two ends of the anti-fl...
PUM
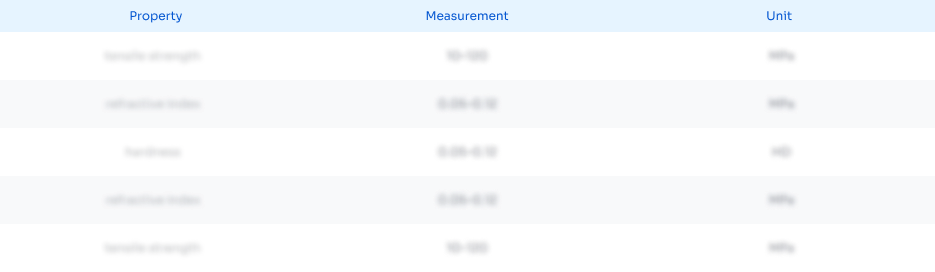
Abstract
Description
Claims
Application Information

- R&D
- Intellectual Property
- Life Sciences
- Materials
- Tech Scout
- Unparalleled Data Quality
- Higher Quality Content
- 60% Fewer Hallucinations
Browse by: Latest US Patents, China's latest patents, Technical Efficacy Thesaurus, Application Domain, Technology Topic, Popular Technical Reports.
© 2025 PatSnap. All rights reserved.Legal|Privacy policy|Modern Slavery Act Transparency Statement|Sitemap|About US| Contact US: help@patsnap.com