Friction material for drum brake of nine-seat passenger vehicle and preparation method of drum brake block
A drum brake and friction material technology, applied in the field of materials, can solve the problems of not being able to carry out large-scale sales activities, difficult to meet market demand, unable to develop brakes, etc., to achieve high parking brake efficiency factors, improve The effect of driving and parking efficiency, good service braking torque and efficiency factors
- Summary
- Abstract
- Description
- Claims
- Application Information
AI Technical Summary
Problems solved by technology
Method used
Image
Examples
Example Embodiment
[0023] Example 1:
[0024] Material equipment: phenolic resin 10.5%, friction powder 4%, rubber powder 4%, aramid fiber 3%, mineral fiber 15%, brass fiber 4%, glass fiber 4%, barite 33%, alumina 5% , Chromite powder 4%, brown corundum 1.75%, graphite 2%, metal sulfide 3.5%, zeolite 3.5%, coke powder 2%, release agent 0.5%, carbon black 0.5%.
[0025] Drum brake pad preparation: Weigh the raw materials according to the above-mentioned weight ratio, and adopt the dry hot pressing process to proceed in the following four steps:
[0026] (1) Mixing: Weigh all the raw materials according to the weight percentage of the formula, put all the materials into the high-speed mixer, and stir for 2 minutes to make the friction material mixture;
[0027] (2) Hot pressing: Put the mixed material into the mold, the mold temperature is controlled at 150±5℃, the pressing pressure is 22±2MPa, and the holding time is 30s / mm for hot pressing; the hot pressing starts 15s, and then The interval is 10s, eac...
Example Embodiment
[0030] Example 2:
[0031] Material equipment: phenolic resin 11.5%, friction powder 4%, aramid fiber 3%, mineral fiber 15%, brass fiber 4%, glass fiber 4%, barite 38%, alumina 5%, chromite powder 4%, brown corundum 1.5%, graphite 3%, coke powder 6%, release agent 0.5%, carbon black 1%.
[0032] Weigh various raw materials according to the above-mentioned weight ratio, and prepare drum brake pads in the same process as in Example 1.
PUM
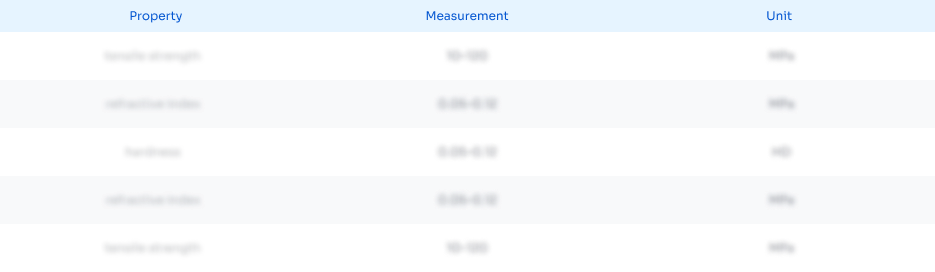
Abstract
Description
Claims
Application Information

- R&D
- Intellectual Property
- Life Sciences
- Materials
- Tech Scout
- Unparalleled Data Quality
- Higher Quality Content
- 60% Fewer Hallucinations
Browse by: Latest US Patents, China's latest patents, Technical Efficacy Thesaurus, Application Domain, Technology Topic, Popular Technical Reports.
© 2025 PatSnap. All rights reserved.Legal|Privacy policy|Modern Slavery Act Transparency Statement|Sitemap|About US| Contact US: help@patsnap.com