Thermal-insulation wear-resistant hydrophobic glass
A hydrophobic glass and thermal insulation technology, which is applied in the direction of glass/slag layered products, synthetic resin layered products, layered products, etc., can solve the problems of reduced hydrophobic performance of glass, difficult coating of hydrophobic film, poor wear resistance of hydrophobic film, etc. , to achieve the effect of maintaining hydrophobic performance, good thermal insulation performance, good hydrophobicity and wear resistance
- Summary
- Abstract
- Description
- Claims
- Application Information
AI Technical Summary
Problems solved by technology
Method used
Image
Examples
Embodiment Construction
[0017] see figure 1 , a kind of thermal insulation wear-resistant hydrophobic glass of the present invention, it comprises glass substrate 1, and described glass substrate 1 front is provided with resin layer 2, and described resin layer 2 is provided with micro-nano structure layer 3, and described micro-nano structure layer 3 A hydrophobic modification layer 4 is arranged on it, the resin layer 2 adopts epoxy resin, unsaturated resin or phenolic resin, the micro-nano structure layer 3 adopts a silicon dioxide micro-nano layer structure layer, and the hydrophobic modification layer 4 Made of trimethylchlorosilane, heptadecylfluorodecyltrimethoxysilane, perfluoroalkylchlorosilane or perfluoroalkylalkoxysilane, the glass substrate 1 is provided with a high reflection layer 5 on the back.
PUM
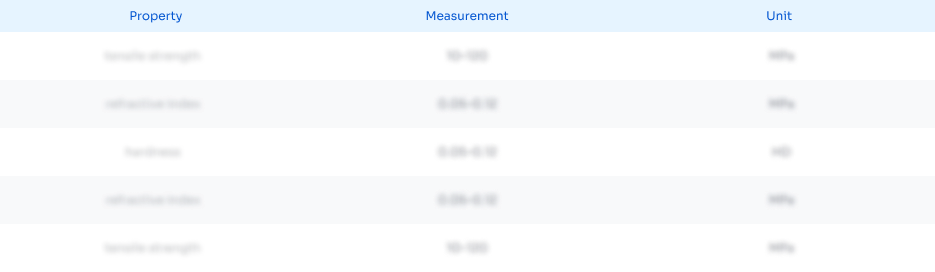
Abstract
Description
Claims
Application Information

- R&D Engineer
- R&D Manager
- IP Professional
- Industry Leading Data Capabilities
- Powerful AI technology
- Patent DNA Extraction
Browse by: Latest US Patents, China's latest patents, Technical Efficacy Thesaurus, Application Domain, Technology Topic, Popular Technical Reports.
© 2024 PatSnap. All rights reserved.Legal|Privacy policy|Modern Slavery Act Transparency Statement|Sitemap|About US| Contact US: help@patsnap.com