Contact Grouting Arrangement Structure and Grouting Method for Steel Substrate of Water Conveyance Tunnel
A technology for water conveyance tunnels and bottom contact, which is applied in infrastructure engineering, hydropower generation, water conservancy engineering, etc., can solve the problems of poor grouting effect, large construction interference, and large number of grouting, so as to improve grouting density and save engineering costs. , the effect of simple construction process
- Summary
- Abstract
- Description
- Claims
- Application Information
AI Technical Summary
Problems solved by technology
Method used
Image
Examples
Embodiment 1
[0028] Such as image 3 As shown, the steel lining 1 is a high-strength steel lining, and the specific implementation steps are as follows:
[0029] 1. Embedding of grouting pipe 4: take 30-50m as a grouting section (subject to good control of grouting pressure and grouting quality), and lay grouting in each grouting section close to the outer wall of the steel lining 1 bottom plate. Both the pipe 4 and the slurry inlet pipe pass through the slurry hole 3 at the bottom of the stiffening ring 2; the slurry inlet pipe 4 does not use a conventional seamless steel pipe, but chooses a commercially available one that has been used in some hydropower projects A special grouting pipe (such as FUKO pipe) material that can discharge slurry along the entire pipe section, and can only discharge slurry but not enter slurry;
[0030] 2. Embedding of exhaust and grout return pipe 5: In consideration of ensuring the quality of contact grouting and minimizing the number of buried pipes, an ex...
Embodiment 2
[0033] Such as Figure 4 As shown, the steel lining is a low-alloy steel lining, and the specific implementation steps are as follows:
[0034] 1. For low alloy steel lining (standard tensile strength is less than 540N / mm 2 ), taking 30-50m as a grouting section (subject to the fact that the grouting pressure and grouting quality can be well controlled), since the steel lining 1 can be opened, in each grouting section, every 5-8m on the bottom plate of the steel lining 1 Open a reserved hole 1-1, and set plugs and plugs in the reserved holes (reserved holes 1-1 can refer to the consolidation grouting holes to set up plugs, plugs and other components);
[0035] 2. Embedding of the grout inlet pipe 4: In each grouting section, the grout inlet pipe 4 is laid along the outer wall of the bottom plate of the steel lining 1, and the grout inlet pipe 4 passes through the grout hole 3 at the bottom of the stiffening ring 2;
[0036] 3. Embedding of the exhaust and grout return pipe 5...
PUM
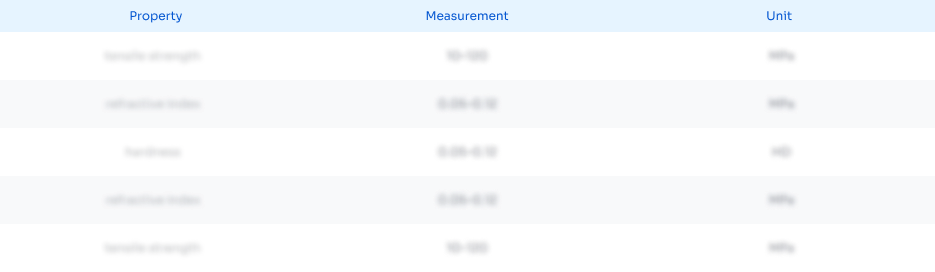
Abstract
Description
Claims
Application Information

- R&D
- Intellectual Property
- Life Sciences
- Materials
- Tech Scout
- Unparalleled Data Quality
- Higher Quality Content
- 60% Fewer Hallucinations
Browse by: Latest US Patents, China's latest patents, Technical Efficacy Thesaurus, Application Domain, Technology Topic, Popular Technical Reports.
© 2025 PatSnap. All rights reserved.Legal|Privacy policy|Modern Slavery Act Transparency Statement|Sitemap|About US| Contact US: help@patsnap.com