Automotive instrument panel composite with high weather resistance and preparation method of composite
A technology of automobile instrument panel and composite material, which is applied in the field of high weather-resistant automobile instrument panel composite material and its preparation field, can solve the problems of weak anti-oxidation ability, poor weather resistance of plastic instrument panel, affecting the appearance and use of automobile interiors, and the like. The effect of low cost, light weight and high strength
- Summary
- Abstract
- Description
- Claims
- Application Information
AI Technical Summary
Problems solved by technology
Method used
Examples
Embodiment 1
[0019] A preparation method of a high weather resistance automotive instrument panel composite material, said method comprising the following steps:
[0020] a. Take raw materials according to the following parts by weight: 6630 parts of nylon, 1255 parts of nylon, 5 parts of shell powder, 6 parts of citraconic anhydride, 5 parts of ammonium tungstate, 4 parts of coconut oil alkyd resin, methacrylic acid hexafluoro 3 parts of butyl ester, 2 parts of zinc stearate, 2 parts of antioxidant, 5 parts of phenylenedi-isooctyl phosphite, 4 parts of magnesium carbonate, 1 part of coupling agent, 1 part of lubricant, 20 parts of organic clay;
[0021] b. Turn on the high-speed mixer, put all the raw materials in step a into the high-speed mixer, adjust the temperature of the high-speed mixer to 130-155°C, and stir for 30 minutes at the speed of the high-speed mixer at 300r / min;
[0022] c. Melt and extrude the material stirred in step b in a twin-screw extruder, set the processing tempe...
Embodiment 2
[0028] A preparation method of a high weather resistance automotive instrument panel composite material, said method comprising the following steps:
[0029] a. Take raw materials according to the following parts by weight: 6640 parts of nylon, 1275 parts of nylon, 13 parts of shell powder, 11 parts of citraconic anhydride, 12 parts of ammonium tungstate, 10 parts of coconut oil alkyd resin, methacrylic acid hexafluoro 10 parts of butyl ester, 3 parts of zinc stearate, 5 parts of antioxidant, 10 parts of monophenylene diisooctyl phosphite, 6 parts of magnesium carbonate, 5 parts of coupling agent, 3 parts of lubricant, 25 parts of organic clay;
[0030] b. Turn on the high-speed mixer, put all the raw materials in step a into the high-speed mixer, adjust the temperature of the high-speed mixer to 130-155°C, and stir for 30 minutes at the speed of the high-speed mixer at 300r / min;
[0031] c. Melt and extrude the material stirred in step b in a twin-screw extruder, set the proc...
Embodiment 3
[0037] A preparation method of a high weather resistance automotive instrument panel composite material, said method comprising the following steps:
[0038] a. Take raw materials according to the following parts by weight: 6635 parts of nylon, 1265 parts of nylon, 9 parts of shell powder, 8 parts of citraconic anhydride, 8 parts of ammonium tungstate, 7 parts of coconut oil alkyd resin, hexafluoromethacrylate 6 parts of butyl ester, 3 parts of zinc stearate, 4 parts of antioxidant, 7 parts of phenylenedioctyl phosphite, 5 parts of magnesium carbonate, 3 parts of coupling agent, 2 parts of lubricant, 23 parts of organic clay;
[0039] b. Turn on the high-speed mixer, put all the raw materials in step a into the high-speed mixer, adjust the temperature of the high-speed mixer to 130-155°C, and stir for 30 minutes at the speed of the high-speed mixer at 300r / min;
[0040] c. Melt and extrude the material stirred in step b in a twin-screw extruder, set the processing temperature ...
PUM
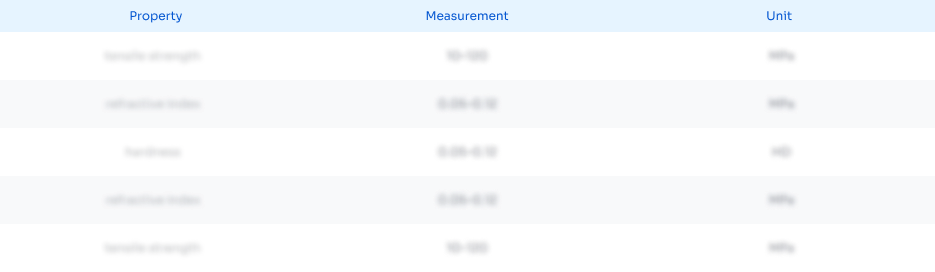
Abstract
Description
Claims
Application Information

- R&D
- Intellectual Property
- Life Sciences
- Materials
- Tech Scout
- Unparalleled Data Quality
- Higher Quality Content
- 60% Fewer Hallucinations
Browse by: Latest US Patents, China's latest patents, Technical Efficacy Thesaurus, Application Domain, Technology Topic, Popular Technical Reports.
© 2025 PatSnap. All rights reserved.Legal|Privacy policy|Modern Slavery Act Transparency Statement|Sitemap|About US| Contact US: help@patsnap.com