Method for producing alumina by sintering lime of sulfur-containing bauxite
A technology of lime sintering and bauxite, which is applied in the direction of alumina/hydroxide, etc., can solve the problems of undisclosed sulfur element hazards, low alumina dissolution rate, and low concentration of dissolution liquid, and achieve low raw material cost and high sintering temperature. The effect of reducing and desulfurization process is simple
- Summary
- Abstract
- Description
- Claims
- Application Information
AI Technical Summary
Problems solved by technology
Method used
Image
Examples
Embodiment 1
[0040] The mass percentage is: Al 2 o 3 55.5%, SiO 2 21.8%, Fe 2 o 3 7.5%, the rest is impurities, and the sulfur-containing low-grade bauxite is crushed and ground to a particle size of less than 200 mesh, accounting for more than 85%. Add limestone and desulfurization slag according to the calcium ratio C / A=1.0. The mass percentage of each element in limestone is: CaO 50.9%, MgO 1.2%, and the rest are impurities; the mass percentage of each element in desulfurization slag is: CaO 42.2% , SO 3 49.2%, of which the amount of desulfurization slag added is 9.0% of the total mass of sulfur-containing bauxite and limestone.
[0041] After the raw materials are mixed evenly according to the proportion, they are kept at 1300 degrees Celsius for 15 minutes, and then naturally cooled in the furnace. The clinker obtained by sintering was subjected to alumina dissolution, the dissolution temperature was 75°C, the time was 30 minutes, and the concentration of sodium carbonate so...
Embodiment 2
[0043] The mass percentage is: Al 2 o 3 36.3%, SiO 2 24.8%, Fe 2 o 3 12.4%, the rest is impurities, and the sulfur-containing low-grade bauxite is crushed and ground to a particle size of less than 200 mesh, accounting for more than 85%. Add limestone and desulfurization slag according to the calcium ratio C / A=0.8. The mass percentage of each element in limestone is: CaO 52.1%, MgO 1.0%, and the rest are impurities; the mass percentage of each element in desulfurization slag is: CaO 43.3% , SO 3 45.2%, of which the amount of desulfurization slag added is 3.5% of the total mass of sulfur-containing bauxite and limestone.
[0044] After mixing the raw materials evenly according to the proportion, keep the temperature at 1250 degrees Celsius for 30 minutes, and then cool naturally in the furnace. The clinker obtained by sintering was subjected to alumina dissolution, the dissolution temperature was 60°C, the time was 15 minutes, and the concentration of sodium carbonate...
Embodiment 3
[0046] The mass percentage is: Al 2 o 3 41.1%, SiO 2 11.0%, Fe 2 o 3 10.3%, the rest is impurities, and the sulfur-containing low-grade bauxite is crushed and ground to a particle size of less than 200 mesh, accounting for more than 85%. Add limestone and desulfurization slag according to the calcium ratio C / A=0.95. The mass percentage of each element in limestone is: CaO 54.6%, MgO 0.7%, and the rest are impurities; the mass percentage of each element in desulfurization slag is: CaO 44.6% , SO 3 40.8%, of which the amount of desulfurization slag added is 6.8% of the total mass of sulfur-containing bauxite and limestone.
[0047] After the raw materials are mixed evenly according to the proportion, they are kept at 1150 degrees Celsius for 60 minutes, and then naturally cooled in the furnace. The clinker obtained by sintering was subjected to alumina dissolution, the dissolution temperature was 70°C, the time was 20 minutes, and the concentration of sodium carbonate ...
PUM
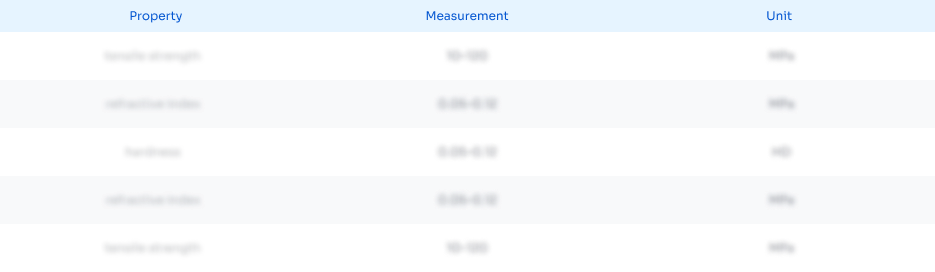
Abstract
Description
Claims
Application Information

- R&D Engineer
- R&D Manager
- IP Professional
- Industry Leading Data Capabilities
- Powerful AI technology
- Patent DNA Extraction
Browse by: Latest US Patents, China's latest patents, Technical Efficacy Thesaurus, Application Domain, Technology Topic, Popular Technical Reports.
© 2024 PatSnap. All rights reserved.Legal|Privacy policy|Modern Slavery Act Transparency Statement|Sitemap|About US| Contact US: help@patsnap.com