A dual-motor constant power synchronous control system without rigid shaft connection
A synchronous control and dual-motor technology, which is applied in the control system, AC motor control, multiple motor speed adjustment, etc., can solve the problems of large load, out-of-synchronization of the output shaft position, and the inability to use constant power control, etc., to improve work efficiency , to ensure the effect of position synchronization
- Summary
- Abstract
- Description
- Claims
- Application Information
AI Technical Summary
Problems solved by technology
Method used
Image
Examples
Embodiment Construction
[0017] The present invention will be further described below in conjunction with the accompanying drawings and embodiments.
[0018] A dual-motor constant power synchronous control system without rigid shaft connection in this embodiment ( figure 1 ), including a master inverter 15 for driving the master motor 5 and a slave inverter 16 for driving the slave motor 12, the master inverter 15 includes a master maximum speed command generating unit 1, a master speed PI regulator 2, a master position control limiter Unit 3, master position control proportional unit 4, master speed variable position integral model 6, master load detection unit 7, slave frequency converter 16 including slave maximum speed command generation unit 8, slave maximum load judging unit 9, slave load detection Unit 10, slave speed PI regulator 11, slave speed variable position integral model 13. Apply this system to two motors to jointly lift the same heavy object with uneven mass distribution 14( figure...
PUM
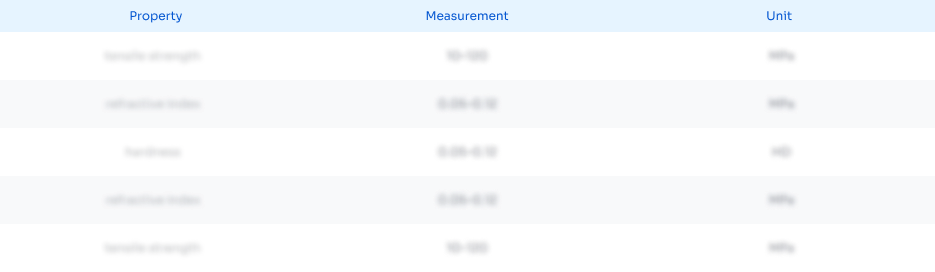
Abstract
Description
Claims
Application Information

- R&D Engineer
- R&D Manager
- IP Professional
- Industry Leading Data Capabilities
- Powerful AI technology
- Patent DNA Extraction
Browse by: Latest US Patents, China's latest patents, Technical Efficacy Thesaurus, Application Domain, Technology Topic, Popular Technical Reports.
© 2024 PatSnap. All rights reserved.Legal|Privacy policy|Modern Slavery Act Transparency Statement|Sitemap|About US| Contact US: help@patsnap.com