Pipe-bending forming mechanism in pipe bending machine
A technology of forming mechanism and pipe bending machine, which is applied in metal processing equipment, feeding device, positioning device, etc., can solve the problems of clamping mold and wheel mold damage, mold clamping too tight or too loose, affecting the quality of bending pipe, etc. Achieve the effect of ensuring molding quality, reducing maintenance costs and improving work efficiency
- Summary
- Abstract
- Description
- Claims
- Application Information
AI Technical Summary
Problems solved by technology
Method used
Image
Examples
Embodiment Construction
[0021] The technical solutions of the present invention will be further described in detail below in conjunction with the accompanying drawings and preferred embodiments.
[0022] Such as figure 1 , figure 2 , image 3As shown, the pipe bending forming mechanism in the pipe bending machine includes: a casing 1, a main shaft 16 is movably supported in the casing 1, and the main shaft 16 is arranged in a horizontal direction. Installed on the casing 1, the front end of the main shaft 16 is provided with an elbow arm 11. Under the action of the main driving mechanism 2, the main shaft 16 can rotate around its own central axis so as to drive the elbow arm 11 to rotate synchronously. In this embodiment, the main driving mechanism 2 includes a large gear 21 fixedly sleeved on the main shaft 16, and a matching curved pipe rack 22 is provided on the large gear 21, and the back of the curved pipe rack 22 is installed Pressed by the large rack press seat 23 in the casing 1, the larg...
PUM
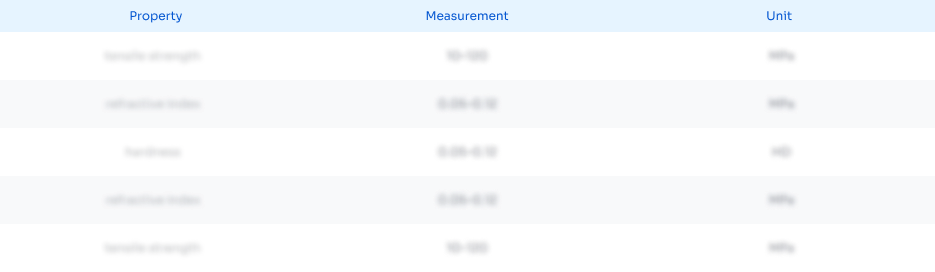
Abstract
Description
Claims
Application Information

- R&D Engineer
- R&D Manager
- IP Professional
- Industry Leading Data Capabilities
- Powerful AI technology
- Patent DNA Extraction
Browse by: Latest US Patents, China's latest patents, Technical Efficacy Thesaurus, Application Domain, Technology Topic, Popular Technical Reports.
© 2024 PatSnap. All rights reserved.Legal|Privacy policy|Modern Slavery Act Transparency Statement|Sitemap|About US| Contact US: help@patsnap.com