A Drilling and Measuring Integrated Device Based on Stress Relief Method
A stress relief method and drilling and testing technology, applied in surveying, drilling equipment, earthwork drilling, etc., can solve the problems of complicated testing process and hinder application, and achieve the effect of simple structural system, reduced requirements, and simple mechanical structure
- Summary
- Abstract
- Description
- Claims
- Application Information
AI Technical Summary
Problems solved by technology
Method used
Image
Examples
Embodiment Construction
[0039]Below in conjunction with accompanying drawing and implementation example, the present invention is further described:
[0040] An integrated device for drilling and measuring based on a stress relief method, comprising a cylindrical relief hole drill part 1, a detachment control part 2 and a measuring hole drill part 3,
[0041] The hole-releasing drill bit part 1 includes a cylindrical drill rod 12, the inner side of the drill rod 12 is provided with a transmission tooth 121, and the bottom of the drill rod 12 is provided with a hole-releasing drill bit 11,
[0042] The measuring hole drill bit part 3 includes a cylindrical casing 34 , an annular positioning part 36 is sleeved on the casing 34 , and a guide groove 343 is formed on the outer side of the annular positioning part 36 along the longitudinal direction of the casing 34 , and the guide groove 343 penetrates through the annular positioning part 36 . On the upper and lower surfaces, the outer side of the annular...
PUM
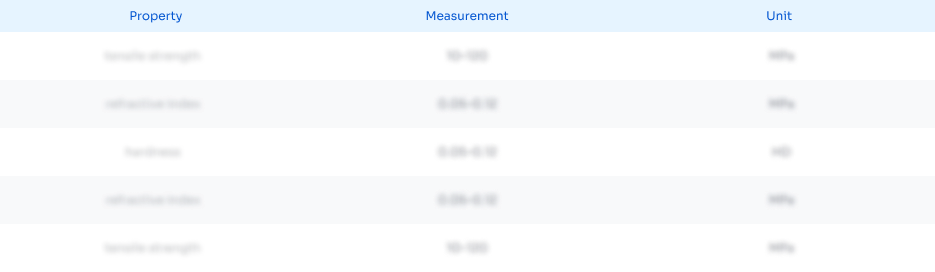
Abstract
Description
Claims
Application Information

- R&D
- Intellectual Property
- Life Sciences
- Materials
- Tech Scout
- Unparalleled Data Quality
- Higher Quality Content
- 60% Fewer Hallucinations
Browse by: Latest US Patents, China's latest patents, Technical Efficacy Thesaurus, Application Domain, Technology Topic, Popular Technical Reports.
© 2025 PatSnap. All rights reserved.Legal|Privacy policy|Modern Slavery Act Transparency Statement|Sitemap|About US| Contact US: help@patsnap.com