Steel strip degreasing process
A degreasing process and technology for steel strips, applied in the field of degreasing of steel strips, can solve the problems of difficulty in meeting the needs of high-grade tin plating production, low efficiency, and high residual debris on the surface of steel strips, so as to improve the efficiency of oil pollution removal, high investment returns, The overall process is simple and easy to implement
- Summary
- Abstract
- Description
- Claims
- Application Information
AI Technical Summary
Problems solved by technology
Method used
Examples
Embodiment 1
[0036] A steel strip degreasing process, comprising the following steps:
[0037] Step A: pre-cleaning the steel strip, using 2% NaOH solution for pre-cleaning, and the pre-cleaning temperature is 50°C.
[0038] Step B: chemical degreasing, using a degreasing solution with a concentration of 2%, and the degreasing temperature is 50°C. The degreasing solution is prepared with low-foaming degreasing powder, stirred evenly, and the alkali point is 30g / L.
[0039] Step C: Spray and brush for the first time, use an alkali brush tank, the alkali point is 35g / L, the temperature is 60°C, and the speed of the brush roller is not lower than 1000 rpm.
[0040] Step D: Electrolytic degreasing, electrolysis current 2600A, current density 15A / d㎡, electrode reversed every 30 minutes, alkali point 45g / L, electrolysis temperature 60°C.
[0041] Step E: cleaning section, further comprising:
[0042] Step a: lye cleaning;
[0043] Step b: Spray and scrub for the second time;
[0044] Step c...
Embodiment 2
[0052] A steel strip degreasing process, comprising the following steps:
[0053] Step A: pre-cleaning the steel strip, using 1% NaOH solution for pre-cleaning, and the pre-cleaning temperature is 40°C.
[0054] Step B: chemical degreasing, using a degreasing solution with a concentration of 3%, and the degreasing temperature is 60°C. The degreasing solution is prepared with low-foaming degreasing powder, stirred evenly, and the alkali point is 50g / L.
[0055] Step C: Spray and brush for the first time, use an alkali brush tank, the alkali point is 80g / L, the temperature is 65°C, and the speed of the brush roller is not lower than 1000 rpm.
[0056] Step D: Electrolytic degreasing, electrolysis current 2550A, current density 14A / d㎡, electrode reversed every 30 minutes, alkali point 120g / L, electrolysis temperature 70°C.
[0057] Step E: cleaning section, further comprising:
[0058] Step a: lye cleaning;
[0059] Step b: Spray and scrub for the second time;
[0060] Step ...
Embodiment 3
[0068] A steel strip degreasing process, comprising the following steps:
[0069] Step A: pre-cleaning the steel strip, using a 3% NaOH solution for pre-cleaning, and the pre-cleaning temperature is 60°C.
[0070] Step B: chemical degreasing, using a degreasing solution with a concentration of 4%, and the degreasing temperature is 70°C. The degreasing solution is prepared with low-foaming degreasing powder, stirred evenly, and the alkali point is 70g / L.
[0071] Step C: Spray and brush for the first time, use an alkali brush tank, the alkali point is 90g / L, the temperature is 70°C, and the speed of the brush roller is not lower than 1000 rpm.
[0072] Step D: Electrolytic degreasing, the electrolytic current is 2650A, the current density is 16A / d㎡, the electrode is reversed every 30 minutes, the alkali point is 140g / L, and the electrolytic temperature is 80°C.
[0073] Step E: cleaning section, further comprising:
[0074] Step a: lye cleaning;
[0075] Step b: Spray and s...
PUM
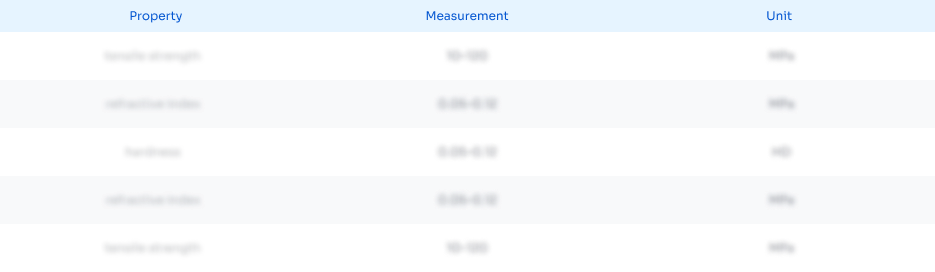
Abstract
Description
Claims
Application Information

- R&D Engineer
- R&D Manager
- IP Professional
- Industry Leading Data Capabilities
- Powerful AI technology
- Patent DNA Extraction
Browse by: Latest US Patents, China's latest patents, Technical Efficacy Thesaurus, Application Domain, Technology Topic, Popular Technical Reports.
© 2024 PatSnap. All rights reserved.Legal|Privacy policy|Modern Slavery Act Transparency Statement|Sitemap|About US| Contact US: help@patsnap.com