Method for controlling microstructure and hot crack sensibility of laser cladding coating
A technology of microstructure and laser cladding, which is applied in the direction of coating, metal material coating process, etc., can solve the problems that there is no method to control the cracks of laser cladding coating, and achieve good effect, simple operation and reliable highly operable effect
- Summary
- Abstract
- Description
- Claims
- Application Information
AI Technical Summary
Problems solved by technology
Method used
Image
Examples
Embodiment Construction
[0038] Such as figure 1 and 2 As shown, a preferred embodiment of the present invention provides a method for controlling the microstructure and thermal crack sensitivity of laser cladding coatings, comprising the following steps:
[0039] Step 1, providing the laser head 1; placing the material 6 for cladding on the surface of the substrate 4;
[0040] Step 2, the laser head emits a high-energy laser beam 2, cladding the material 6 for cladding on the surface of the substrate 4, forming a molten pool 5, and the molten pool 5 solidifies to form a cladding coating 3; wherein, in the cladding process In the process, the laser head 1 is rotated so that the incident angle of the laser light is not perpendicular to the substrate 4, and the incident angle of the laser light is changed.
[0041] Step 3, the change of the incident angle of the laser changes the morphology and temperature field of the molten pool 5, thereby changing the microstructure and growth orientation of the cl...
PUM
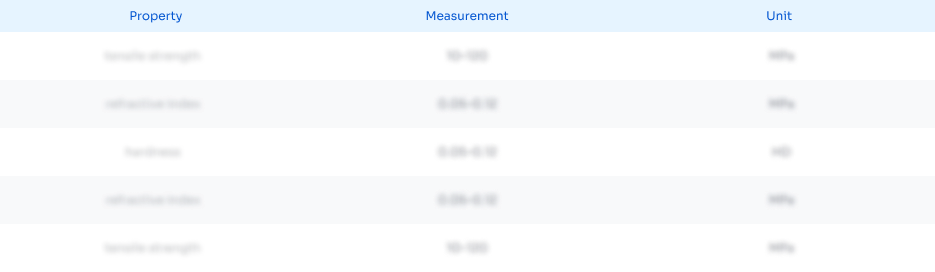
Abstract
Description
Claims
Application Information

- Generate Ideas
- Intellectual Property
- Life Sciences
- Materials
- Tech Scout
- Unparalleled Data Quality
- Higher Quality Content
- 60% Fewer Hallucinations
Browse by: Latest US Patents, China's latest patents, Technical Efficacy Thesaurus, Application Domain, Technology Topic, Popular Technical Reports.
© 2025 PatSnap. All rights reserved.Legal|Privacy policy|Modern Slavery Act Transparency Statement|Sitemap|About US| Contact US: help@patsnap.com