Foaming mold exhaust device and foaming mold with the device
A foaming mold and exhaust device technology, which is applied in the field of exhaust devices, can solve the problems of not being able to install exhaust needles according to process requirements, adding burrs and grinding in the rear, and maintaining high maintenance costs, and achieving product quality. Significant improvement, meeting foaming process requirements and eliminating product shortages
- Summary
- Abstract
- Description
- Claims
- Application Information
AI Technical Summary
Problems solved by technology
Method used
Image
Examples
Embodiment Construction
[0026] The specific implementation manners of the present invention will be further described in detail below in conjunction with the accompanying drawings.
[0027] Such as figure 1 In the foaming mold and its exhaust device shown, both ends of the fixed plate 2 are fixedly connected to the mold 1, the cylinder seat of the cylinder 3 is connected to the fixed plate 2, the T-shaped buckle 8 is connected to the piston rod of the cylinder 3, and the exhaust The needle plate 4 is connected with the T-shaped buckle 8. There are two guide posts 5 on the mold 1. The exhaust needle plate 4 is slidingly connected with the guide posts 5 through the two guide sleeves 6 connected on it. The piston rod of the cylinder 3 is stretched. It can drive the exhaust needle plate 4 to reciprocate along the guide column 5, several exhaust needle steel sleeves 10 are embedded in the mould, several exhaust needles 7 are connected to the exhaust needle plate 4, and the exhaust needles 7 respectively p...
PUM
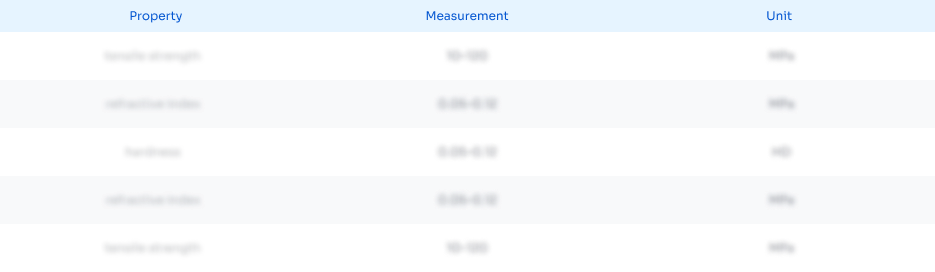
Abstract
Description
Claims
Application Information

- R&D
- Intellectual Property
- Life Sciences
- Materials
- Tech Scout
- Unparalleled Data Quality
- Higher Quality Content
- 60% Fewer Hallucinations
Browse by: Latest US Patents, China's latest patents, Technical Efficacy Thesaurus, Application Domain, Technology Topic, Popular Technical Reports.
© 2025 PatSnap. All rights reserved.Legal|Privacy policy|Modern Slavery Act Transparency Statement|Sitemap|About US| Contact US: help@patsnap.com