Technology used for assembling and welding irradiating supervision pipe
A technology of radiation supervision tube and process, applied in welding equipment, laser welding equipment, manufacturing tools, etc., to achieve the effect of improving assembly and welding efficiency
- Summary
- Abstract
- Description
- Claims
- Application Information
AI Technical Summary
Problems solved by technology
Method used
Image
Examples
Embodiment
[0029] Such as figure 1 As shown, a process for assembling and welding the irradiation supervisory tube in the present invention is carried out on the welding tool. The tooling includes a base made of cast iron with an I-shaped cross section. A connecting piece with a groove is provided in the middle of the connecting piece, and a supporting seat is provided in the connecting piece, and two slopes are arranged on the supporting seat to form a V-shaped groove. Two neck support blocks on a straight line are also provided with a limit reference block between the support base and the neck support block. Formed with an integrated structure, it also includes a four-petal centering member that wraps the irradiation supervision tube. After the four-petal centering member is wrapped on the outside of the irradiation supervision tube, one end is a bottom plug fixed in the rolling assembly on the support seat, and the other end is For the top plug to be placed on the limit reference blo...
PUM
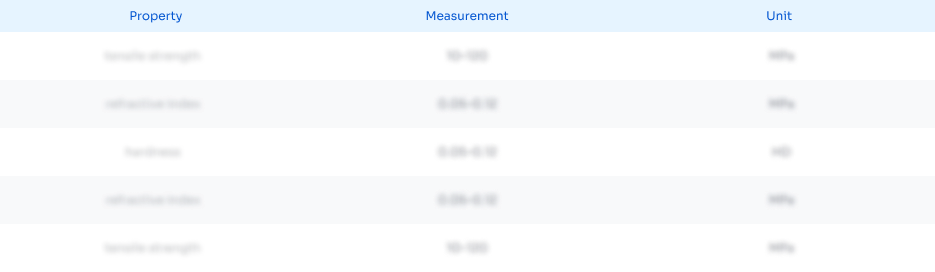
Abstract
Description
Claims
Application Information

- R&D
- Intellectual Property
- Life Sciences
- Materials
- Tech Scout
- Unparalleled Data Quality
- Higher Quality Content
- 60% Fewer Hallucinations
Browse by: Latest US Patents, China's latest patents, Technical Efficacy Thesaurus, Application Domain, Technology Topic, Popular Technical Reports.
© 2025 PatSnap. All rights reserved.Legal|Privacy policy|Modern Slavery Act Transparency Statement|Sitemap|About US| Contact US: help@patsnap.com