Continuous casting blank section casting cold material placing structure and placing method thereof
A continuous casting slab and cold material technology, which is applied to the placement structure of the continuous casting slab section and its placement field, and can solve the problem of continuous casting slab dragging, leakage, large economic losses, production accidents, leakage, etc. question
- Summary
- Abstract
- Description
- Claims
- Application Information
AI Technical Summary
Problems solved by technology
Method used
Image
Examples
Embodiment Construction
[0030] Specific embodiments of the present invention will be described in detail below in conjunction with the accompanying drawings. It should be understood that the specific embodiments described here are only used to illustrate and explain the present invention, not to limit the present invention.
[0031] In the present invention, in the absence of a contrary statement, the orientation words included in the term such as "up, down, left, right, inside, outside" only represent the orientation of the term in the normal use state, or for the purpose of A common term understood by those skilled in the art, and should not be considered as a limitation of the term.
[0032] The invention provides a placement structure for the cold material poured on the end face of the continuous casting slab, such as figure 1 , figure 2 , image 3 , Figure 4 and Figure 5 As shown, the placement structure includes a crystallizer 3, a dummy head arranged inside the crystallizer 3, and the ...
PUM
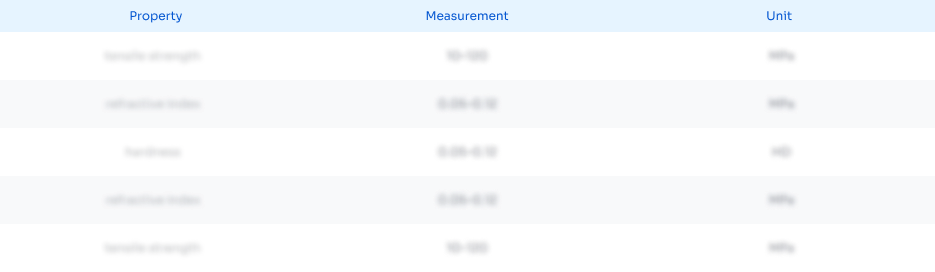
Abstract
Description
Claims
Application Information

- Generate Ideas
- Intellectual Property
- Life Sciences
- Materials
- Tech Scout
- Unparalleled Data Quality
- Higher Quality Content
- 60% Fewer Hallucinations
Browse by: Latest US Patents, China's latest patents, Technical Efficacy Thesaurus, Application Domain, Technology Topic, Popular Technical Reports.
© 2025 PatSnap. All rights reserved.Legal|Privacy policy|Modern Slavery Act Transparency Statement|Sitemap|About US| Contact US: help@patsnap.com