A kind of manufacturing method of anode
A manufacturing method and anode technology, applied in capacitor electrodes, capacitors, circuits, etc., can solve the problems of low product capacity extraction rate, local pelletization of tantalum powder, dead holes in pellets, etc., to reduce friction and reduce dead holes. "Proportion, the effect of improving liquidity
- Summary
- Abstract
- Description
- Claims
- Application Information
AI Technical Summary
Problems solved by technology
Method used
Image
Examples
Embodiment 1
[0028] Tantalum powder with a specific volume of 100000 μF·V / g was used to press into an anode block with a powder weight of 26 mg and a size of 1.16 mm×2.35 mm×1.75 mm. The specific steps are: take 5 g of polycarbonate with a molecular weight of 200,000 and dissolve it in 65 g of acetone, and stir it evenly for later use; mix the polycarbonate solution with 200 g of tantalum powder, place it in a rotary agitator, and stir it at 60°C for 2 hours; Import the mixed tantalum powder into the powder tank of the molding machine, and continuously press the anode block; put the formed anode block into the sintering furnace, dewax at 400°C for 30 minutes, then heat up to the firing temperature for 20 minutes for sintering, and then cool Below 50°C, form an anode and put it in a vacuum drying dish to cool to room temperature for later use.
Embodiment 2
[0030] Tantalum powder with a specific volume of 120000 μF·V / g was used to press into an anode block with a powder weight of 26 mg and a size of 1.15 mm×2.35 mm×1.75 mm. The specific steps are: take 6g of polycarbonate with a molecular weight of 300,000 and dissolve it in 94g of acetone, stir well for later use; mix the polycarbonate solution with 200g of tantalum powder evenly, place it in a rotary stirrer, and stir at 60°C for 2 hours; Import the mixed tantalum powder into the powder tank of the molding machine, and continuously press the anode block; put the formed anode block into the sintering furnace, dewax at 400°C for 30 minutes, then heat up to the firing temperature for 20 minutes for sintering, and then cool Below 50°C, form an anode and put it in a vacuum drying dish to cool to room temperature for later use.
Embodiment 3
[0032] Tantalum powder with a specific volume of 150000 μF·V / g was used to press into an anode block with a powder weight of 9.8 mg and a size of 1.04 mm×1.20 mm×1.40 mm. The specific steps are: take 8 g of polycarbonate with a molecular weight of 300,000 and dissolve it in 92 g of acetone, and stir it evenly for later use; mix the polycarbonate solution with 200 g of tantalum powder, place it in a rotary agitator, and stir it at 60°C for 2 hours; Import the mixed tantalum powder into the powder tank of the molding machine, and continuously press the anode block; put the formed anode block into the sintering furnace, dewax at 400°C for 30 minutes, then heat up to the firing temperature for 20 minutes for sintering, and then cool Below 50°C, form an anode and put it in a vacuum drying dish to cool to room temperature for later use.
PUM
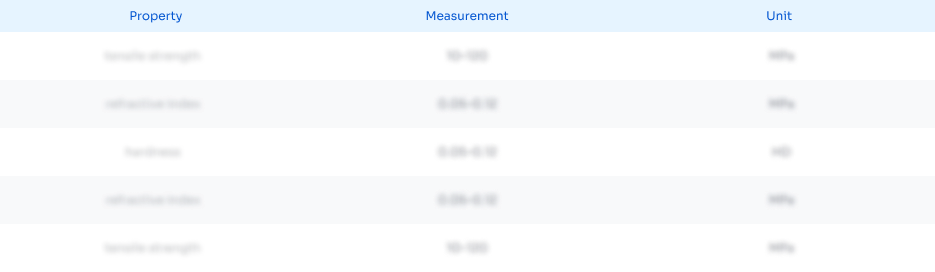
Abstract
Description
Claims
Application Information

- Generate Ideas
- Intellectual Property
- Life Sciences
- Materials
- Tech Scout
- Unparalleled Data Quality
- Higher Quality Content
- 60% Fewer Hallucinations
Browse by: Latest US Patents, China's latest patents, Technical Efficacy Thesaurus, Application Domain, Technology Topic, Popular Technical Reports.
© 2025 PatSnap. All rights reserved.Legal|Privacy policy|Modern Slavery Act Transparency Statement|Sitemap|About US| Contact US: help@patsnap.com