High-speed train traction transmission control system real-time fault simulation platform
A traction drive control, high-speed train technology, applied in the field of fault injection and signal processing, and semi-physical simulation of high-speed train traction drive control system, can solve problems such as real-time simulation of failure operation behavior of traction drive control system, and achieve strong applicability. Effect
- Summary
- Abstract
- Description
- Claims
- Application Information
AI Technical Summary
Problems solved by technology
Method used
Image
Examples
Embodiment Construction
[0044] The present invention will be further described below in conjunction with the accompanying drawings and embodiments.
[0045] The high-speed train traction drive control system includes traction transformer, traction converter (rectifier, intermediate DC circuit and inverter), traction motor, sensor, traction drive control unit TCU and other components. The real-time fault simulation platform can realize the normal modeling and fault modeling of the high-speed train traction drive control system, as well as the real-time simulation of normal operation behavior and fault operation behavior.
[0046] figure 1 A schematic structural diagram of a real-time fault simulation platform for a high-speed train traction drive control system of the present invention is given. The real-time fault simulation platform includes a real-time simulator, a fault injection unit FIU, a physical traction drive control unit TCU, and a real-time data acquisition and monitoring unit.
[0047] T...
PUM
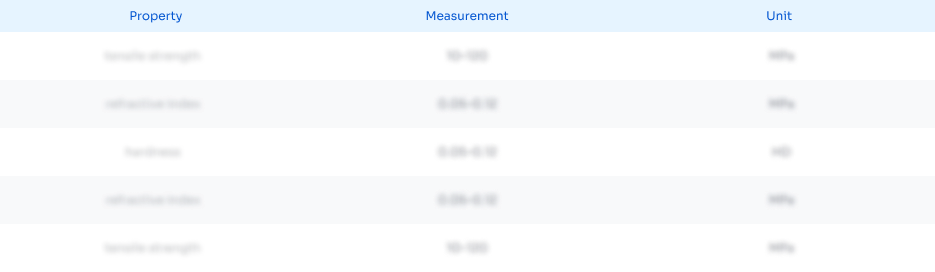
Abstract
Description
Claims
Application Information

- R&D
- Intellectual Property
- Life Sciences
- Materials
- Tech Scout
- Unparalleled Data Quality
- Higher Quality Content
- 60% Fewer Hallucinations
Browse by: Latest US Patents, China's latest patents, Technical Efficacy Thesaurus, Application Domain, Technology Topic, Popular Technical Reports.
© 2025 PatSnap. All rights reserved.Legal|Privacy policy|Modern Slavery Act Transparency Statement|Sitemap|About US| Contact US: help@patsnap.com