Robot harmonic reducer device
A harmonic reducer and robot technology, applied in the direction of transmission devices, friction transmission devices, mechanical equipment, etc., can solve the problems of large assembly errors, reduced assembly accuracy, and low power output accuracy, and achieve the goal of saving raw materials and improving assembly accuracy Effect
- Summary
- Abstract
- Description
- Claims
- Application Information
AI Technical Summary
Problems solved by technology
Method used
Image
Examples
Embodiment Construction
[0030] Examples such as Figure 2-4 As shown, a robot harmonic reducer device includes a rigid spline 1, a flexible spline 5 and a wave generator 2 assembled together; a coaxial positioning device is arranged between the flexible spline 5 and the wave generator 2.
[0031] The coaxial positioning device includes a positioning shaft 9 extending toward the flexspline 5 along the central axis of the wave generator 2 , and the rear end of the positioning shaft 9 is connected to the flexspline 5 through a deep groove ball bearing 8 rotatably supported.
[0032] The rear end of the positioning shaft 9 is integrally processed with a bearing mounting table 13, the deep groove ball bearing 8 is installed on the bearing mounting table 13, and the position corresponding to the rear end of the positioning shaft 9 on the flexible spline 5 is integrally processed There is a sinker 10 , and the outer end of the deep groove ball bearing 8 is located in the sinker 10 and tightly connected with...
PUM
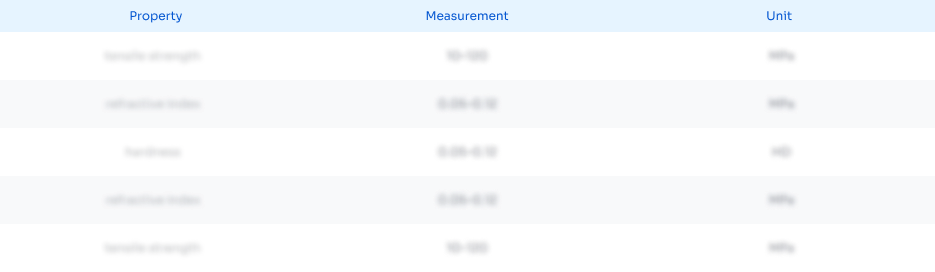
Abstract
Description
Claims
Application Information

- R&D
- Intellectual Property
- Life Sciences
- Materials
- Tech Scout
- Unparalleled Data Quality
- Higher Quality Content
- 60% Fewer Hallucinations
Browse by: Latest US Patents, China's latest patents, Technical Efficacy Thesaurus, Application Domain, Technology Topic, Popular Technical Reports.
© 2025 PatSnap. All rights reserved.Legal|Privacy policy|Modern Slavery Act Transparency Statement|Sitemap|About US| Contact US: help@patsnap.com