A detection method of hydraulic pressure, buoyancy and floating distance
A detection method and pressure technology, which is applied in the field of precision polishing, can solve the problems that the surface quality of the workpiece is difficult to break through, there is no hydraulic pressure detection technology and polishing gap detection technology, and the working conditions and processing parameters cannot be guaranteed, so as to reduce the detection error. , to ensure the effect of accuracy
- Summary
- Abstract
- Description
- Claims
- Application Information
AI Technical Summary
Problems solved by technology
Method used
Image
Examples
Embodiment Construction
[0020] The present invention will be further described below in conjunction with accompanying drawing:
[0021] The force detection is realized by the silicon piezoresistive pressure sensor 8 and the piezoelectric load cell 16, which have high sensitivity, small zero drift, good repeatability and small structure. The four silicon piezoresistive pressure sensors 8 evenly distributed on the bottom of the container adopt an embedded structure, which can meet the requirements of force measurement under a small gap. The piezoelectric load cell 16 is installed at one end of the spline shaft to detect the buoyancy force on the polishing disc; the distance detection consists of three embedded inductive sensors 9 and a grating ruler. The inductive sensor distributed at the bottom of the container has a detection distance as small as 0-1mm and a working frequency of up to kilohertz, which can meet the detection requirements of the polishing gap. The reading head of the grating ruler is...
PUM
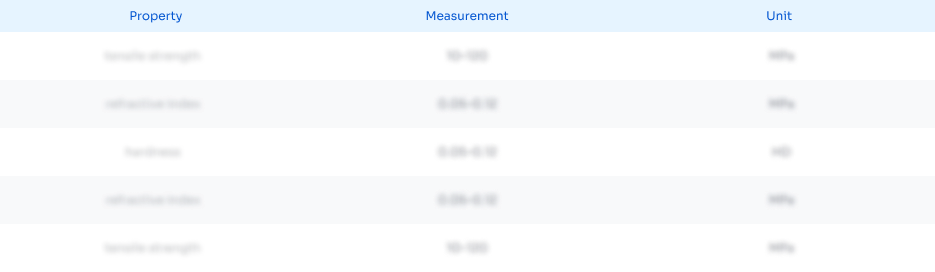
Abstract
Description
Claims
Application Information

- Generate Ideas
- Intellectual Property
- Life Sciences
- Materials
- Tech Scout
- Unparalleled Data Quality
- Higher Quality Content
- 60% Fewer Hallucinations
Browse by: Latest US Patents, China's latest patents, Technical Efficacy Thesaurus, Application Domain, Technology Topic, Popular Technical Reports.
© 2025 PatSnap. All rights reserved.Legal|Privacy policy|Modern Slavery Act Transparency Statement|Sitemap|About US| Contact US: help@patsnap.com