Process for removal of 1,2-epoxy-5-hexene from epichlorohydrin
An epichlorohydrin, epoxy-based technology applied to remove 1 from epichlorohydrin, which can solve problems such as pollution, increased complexity and cost
- Summary
- Abstract
- Description
- Claims
- Application Information
AI Technical Summary
Problems solved by technology
Method used
Image
Examples
Embodiment
[0044] Experimental setup. The simulation experiments were carried out in a jacketed glass reactor with a reaction volume of about 250 ml equipped with temperature control, reflux condenser, overhead stirrer and UV-VIS probe. Here is the addition of 1,2-epoxy-5-hexene to a solution containing a fixed amount of dissolved Cl 2 of pure ECH instead of first preparing epichlorohydrin and dosing Cl based on the 1,2-epoxy-5-hexene contained therein 2 . This has the advantage of reproducibility and facilitates comparison of results.
[0045] By using Hastelloy (Hastelloy) autoclave, the Cl 2 Dissolve in epichlorohydrin and transfer to a glass reactor. During the transfer from the autoclave to the glass reactor, the Cl in epichlorohydrin 2 Concentration is stable. Cl 2 Concentrations were measured by UV-VIS spectrophotometer at a wavelength of 360 nm. The concentrations of 1,2-epoxy-5-hexene and epichlorohydrin were measured by gas chromatography. In a typical example, dissolv...
Embodiment 2-7
[0049] using different temperatures and Cl 2 / 1,2-epoxy-5-hexene ratio, the results of the corresponding reactions are listed in Table 1 (entries 2-7). The reaction time for the exhaustion of the halogen was the same as that of Comparative Example C1, which was less than 5 seconds.
[0050] Table 1. Chlorination of 1,2-epoxy-5-hexene in epichlorohydrin
[0051]
[0052] (*) Calculated based on 1,2-epoxy-5-hexene and other ethylenically unsaturated components in epichlorohydrin
[0053] The reaction proceeds well when the temperature is higher than 30°C, because the Cl 2 It reacts with 1,2-epoxy-5-hexene with high selectivity. Using excess Cl 2 Can result in complete removal of 1,2-epoxy-5-hexene, but also result in excess chlorine present in the product. Comparing Examples 1 (Comparative), 2 and 3 shows that a substantial amount of 1,2-epoxy-5-hexene can be removed using substoichiometric amounts of chlorine. Embodiments 5 to 7 show that high temperatures can be used....
PUM
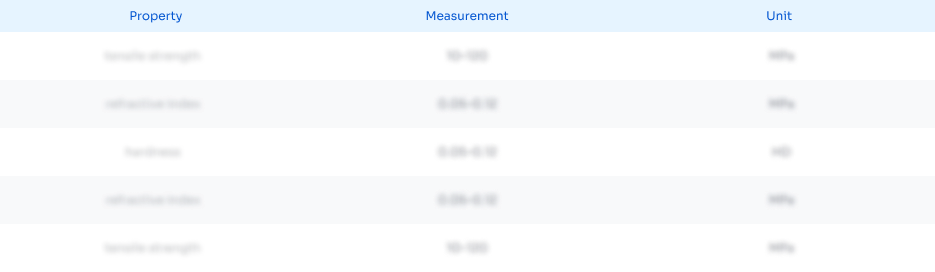
Abstract
Description
Claims
Application Information

- R&D
- Intellectual Property
- Life Sciences
- Materials
- Tech Scout
- Unparalleled Data Quality
- Higher Quality Content
- 60% Fewer Hallucinations
Browse by: Latest US Patents, China's latest patents, Technical Efficacy Thesaurus, Application Domain, Technology Topic, Popular Technical Reports.
© 2025 PatSnap. All rights reserved.Legal|Privacy policy|Modern Slavery Act Transparency Statement|Sitemap|About US| Contact US: help@patsnap.com