A single-probe three-coil maglev train gap sensor with fault location function
A gap sensor and fault location technology, applied in the direction of instruments, electromagnetic means, measuring devices, etc., can solve the problems of inability to install, the frequency of the signal source cannot be the same, reduce the magnetic field interference, etc., to achieve convenient installation, reduce costs, and reduce the size of the probe Effect
- Summary
- Abstract
- Description
- Claims
- Application Information
AI Technical Summary
Problems solved by technology
Method used
Image
Examples
Embodiment Construction
[0019] figure 1 and figure 2 As shown, a specific embodiment of the present invention is: comprising a controllable high-frequency switch connected to the high-frequency signal source on the vehicle body, a probe coil connected to the controllable high-frequency switch, a signal detection circuit connected to the probe coil, A self-diagnosis unit connected to the signal detection circuit; characterized in that the sensor is composed of a single probe, and there are 3 detection coils (L1, L2 and L3) in the probe; the size and winding of the 3 detection coils (L1, L2 and L3) The same direction, and completely overlapped in space; the input terminals of the three detection coils (L1, L2 and L3) are respectively connected to the three high-frequency signal sources (S1, S2) through three controllable high-frequency switches (K1, K2 and K3) and S3); the output terminals of the three detection coils (L1, L2 and L3) are respectively connected to the independent signal detection circ...
PUM
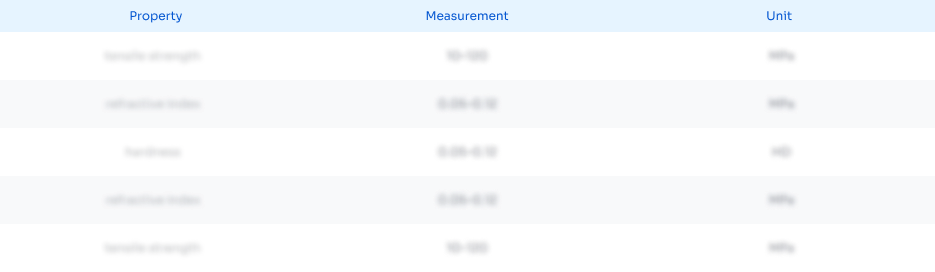
Abstract
Description
Claims
Application Information

- Generate Ideas
- Intellectual Property
- Life Sciences
- Materials
- Tech Scout
- Unparalleled Data Quality
- Higher Quality Content
- 60% Fewer Hallucinations
Browse by: Latest US Patents, China's latest patents, Technical Efficacy Thesaurus, Application Domain, Technology Topic, Popular Technical Reports.
© 2025 PatSnap. All rights reserved.Legal|Privacy policy|Modern Slavery Act Transparency Statement|Sitemap|About US| Contact US: help@patsnap.com