Recycling method for nickel in nickel-cadmium-zinc slag
A recovery method, nickel-cadmium technology, applied in the field of comprehensive recovery and treatment of nickel-cadmium-zinc waste slag, can solve the problems of unfavorable smelting reduction, low nickel recovery rate, low value, etc., achieve complete separation of nickel-cadmium-zinc, high nickel recovery rate, short process effect
- Summary
- Abstract
- Description
- Claims
- Application Information
AI Technical Summary
Benefits of technology
Problems solved by technology
Method used
Examples
Embodiment 1
[0019] (1) Add 1000g of nickel-cadmium-zinc slag containing 63.7% nickel, 1.6% cadmium and 32.3% zinc to 1.24L of 8mol / L sodium hydroxide solution, and leaching at 20°C for 15h;
[0020] (2) The leaching residue is washed with 1mol / L sodium hydroxide solution until the leaching residue contains 0.01% zinc, and then washed with water until the washing water pH=9;
[0021] (3) Obtain 675.2g of leaching slag, the composition of which is Ni94.31%, Cd2.36%, Zn0.01%, O3.13%, smelting the leaching slag in an intermediate frequency furnace at 900°C for 5h, adding 63.4g of charcoal during smelting , the cadmium oxide and nickel oxide in the slag are reduced to simple cadmium and nickel, the volatilized cadmium is recovered in the dust collection equipment, and the recovered cadmium powder is Ni0.003%, Zn0.001%, Cd99.12%;
[0022] (4) After the reduction, the nickel was poured into nickel ingots to obtain 637.2g of nickel ingots, the composition of which was Ni98.99%, Cd0.0078%, Zn0.004...
Embodiment 2
[0024] (1) Add 100kg of nickel-cadmium-zinc slag containing 56.3% nickel, 3.72% cadmium, and 38.9% zinc to 144L of 10mol / L sodium hydroxide solution, and leaching at 40°C for 20h;
[0025] (2) The leaching residue is washed with 2mol / L sodium hydroxide solution until the leaching residue contains 0.07% zinc, and then washed with water until the washing water pH=7;
[0026] (3) Obtain 60.8kg of leaching slag, the composition of which is Ni89.47%, Cd6.05%, Zn0.03%, O3.87%, smelting the leaching slag in an intermediate frequency furnace at 800°C for 3 hours, adding 11.8kg of charcoal during smelting , the cadmium oxide and nickel oxide in the slag are reduced to simple cadmium and nickel, the volatilized cadmium is recovered in the dust collection equipment, and the recovered cadmium powder is Ni0.007%, Zn0.005%, Cd97.72%;
[0027] (4) After the reduction, the nickel was atomized into nickel powder, and 54.1kg of atomized nickel powder was obtained, the composition of which was N...
Embodiment 3
[0029] (1) Add 3000g of nickel-cadmium-zinc slag containing 26.3% nickel, 7.04% cadmium and 43.2% zinc to 4L of 9mol / L sodium hydroxide solution, and leaching at 30°C for 17h;
[0030] (2) The leaching residue is washed with 1.5mol / L sodium hydroxide solution until the leaching residue contains 0.04% zinc, and then washed with water until the washing water pH=8;
[0031] (3) 1371.8g of leaching slag was obtained, the composition of which was Ni56.79%, Cd15.19%, Zn0.035%, O27.14%. The leaching slag was smelted in an intermediate frequency furnace at 850°C for 4 hours, and 1489g of charcoal was added during smelting. The cadmium oxide and nickel oxide in the slag are reduced to simple cadmium and nickel, and the volatilized cadmium is recovered in the dust collection equipment. The recovered cadmium powder is composed of Ni0.017%, Zn0.002%, and Cd98.56%;
[0032] (4) After the reduction, the nickel was atomized into nickel powder, and 785.1g of atomized nickel powder was obtaine...
PUM
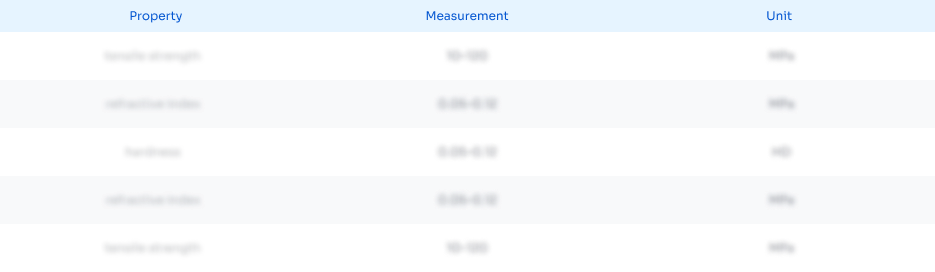
Abstract
Description
Claims
Application Information

- Generate Ideas
- Intellectual Property
- Life Sciences
- Materials
- Tech Scout
- Unparalleled Data Quality
- Higher Quality Content
- 60% Fewer Hallucinations
Browse by: Latest US Patents, China's latest patents, Technical Efficacy Thesaurus, Application Domain, Technology Topic, Popular Technical Reports.
© 2025 PatSnap. All rights reserved.Legal|Privacy policy|Modern Slavery Act Transparency Statement|Sitemap|About US| Contact US: help@patsnap.com