Hollow single screw extruder with spiral grooves in double sides
A single-screw extruder and hollow screw technology, applied in the field of new hollow single-screw extruders, can solve the problems of different and complex structures, and achieve the effects of eliminating poor stability, shortening the length of the screw, and strengthening the drag effect.
- Summary
- Abstract
- Description
- Claims
- Application Information
AI Technical Summary
Problems solved by technology
Method used
Image
Examples
Embodiment 1
[0029] like figure 1 and figure 2 As shown, it is a hollow single-screw extruder with double-sided screw grooves, including a motor 1, a transmission mechanism 2, a seat 3, a radial thrust bearing group 4, a barrel 5, a hollow screw 6, and a heating coil 7 , extruder head 8, hopper 9, gear 10 and central shaft 11; wherein the motor 1 drives the hollow screw 6 to rotate through the transmission mechanism 2 and the gear 10, and the extruder head 8 is located at the bottom of the barrel 5 Discharge end; the hollow screw 6 is located in the barrel 5, the central shaft 11 is located in the hollow screw 6, the hollow screw 6 is coaxial with the barrel 5 and the central shaft 11 and can be rotated relative to each other. An outer helical groove 601 is arranged on the outer circular surface, and an inner helical groove 602 is arranged on the inner circular hole of the hollow screw 6; the first discharge port 901 and the second discharge port 902 of the hopper 9 are connected with th...
Embodiment 2
[0033] like image 3 As shown, it is a hollow single-screw extruder with double-sided screw grooves, including a motor 1, a transmission mechanism 2, a seat 3, a radial thrust bearing group 4, a barrel 5, a hollow screw 6, and a heating coil 7 , extruder head 8, hopper 9, gear 10 and central shaft 11; wherein the motor 1 drives the hollow screw 6 to rotate through the transmission mechanism 2 and the gear 10 ( image 3It is not shown in the figure, and its matching relationship is the same as that of Embodiment 1), the extruder head 8 is set at the discharge end of the barrel 5; the hollow screw 6 is located in the barrel 5, and the central shaft 11 is located in the hollow Inside the screw rod 6, the hollow screw rod 6 is coaxial with the machine barrel 5 and the central shaft 11 and can be rotated relatively. Inner spiral groove 602; the first discharge port 901 and the second discharge port 902 of the hopper 9 communicate with the left end of the inner spiral groove 602 an...
Embodiment 3
[0037] like Figure 4 As shown, it is a hollow single-screw extruder with double-sided screw grooves, including a motor 1, a transmission mechanism 2, a seat 3, a radial thrust bearing group 4, a barrel 5, a hollow screw 6, and a heating coil 7 , extruder head 8, hopper 9, gear 10 and central shaft 11; wherein the motor 1 drives the hollow screw 6 to rotate through the transmission mechanism 2 and the gear 10 ( Figure 4 It is not shown in the figure, and its matching relationship is the same as that of Embodiment 1), the extruder head 8 is set at the discharge end of the barrel 5; the hollow screw 6 is located in the barrel 5, and the central shaft 11 is located in the hollow Inside the screw rod 6, the hollow screw rod 6 is coaxial with the machine barrel 5 and the central shaft 11 and can be rotated relatively. Inner spiral groove 602; the first discharge port 901 and the second discharge port 902 of the hopper 9 communicate with the left end of the inner spiral groove 602...
PUM
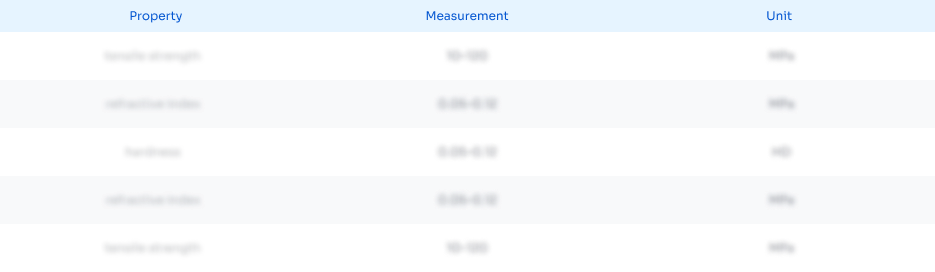
Abstract
Description
Claims
Application Information

- R&D Engineer
- R&D Manager
- IP Professional
- Industry Leading Data Capabilities
- Powerful AI technology
- Patent DNA Extraction
Browse by: Latest US Patents, China's latest patents, Technical Efficacy Thesaurus, Application Domain, Technology Topic, Popular Technical Reports.
© 2024 PatSnap. All rights reserved.Legal|Privacy policy|Modern Slavery Act Transparency Statement|Sitemap|About US| Contact US: help@patsnap.com