Drilling machine parameter monitoring system for distributed data collection
A parameter monitoring and data acquisition module technology, which is applied to the automatic control system of drilling, drilling equipment, earthwork drilling and production, etc., can solve the problems of incomplete monitoring of drilling parameters, easy paralysis of system functions, difficulties in field wiring, etc., and achieve good openness High degree of dispersion, easy installation, and wide range of measurement parameters
- Summary
- Abstract
- Description
- Claims
- Application Information
AI Technical Summary
Problems solved by technology
Method used
Image
Examples
Embodiment 1
[0019] A drilling rig parameter monitoring system for distributed data collection provided by the present invention includes a data processing unit 100 , a driller's floor operation unit 200 , an OPC server 300 and a data collection module 400 . see Figure 1~3 ,in figure 1 A schematic structural view of Embodiment 1 of the drilling rig parameter monitoring device is shown, figure 2 A schematic diagram of the specific structure of the data processing unit 100 in Embodiment 1 is shown, image 3 A specific structural schematic diagram of the data collection module 400 in the first implementation is shown.
[0020] The data processing unit 100 includes a data processing core 110, a data storage unit 120, field bus interfaces 1 to 3 (130, 140 and 150), and a communication interface 4 (160); the data processing unit 100 passes through the bus interface 1 (130 ) is connected with the driller's floor operating unit 200; connected with a plurality of data acquisition modules 400 t...
Embodiment 2
[0035] In order to describe the working principle and implementation of the present invention in detail, on the basis of the technical solution of the first embodiment above, the application of the drilling rig parameter monitoring device of the present invention is exemplified as a further preferred implementation.
[0036] see Figure 4 , Figure 4 A schematic structural diagram of the second embodiment of the drilling rig parameter monitoring system is shown. In this embodiment, the fieldbus interfaces 1-2 and the communication interface 4 of the data processing unit 100 are applied. Drilling operation. The data processing unit 100 is connected to a plurality of data acquisition modules 400 through the CAN bus to obtain the operating parameters of the drilling rig in real time. After processing and storing, the operating parameters and status of the drilling rig are sent to the driller floor operating unit 200 through the field bus interface 1; At the same time, the oper...
Embodiment 3
[0038] see Figure 5 , Figure 5 A schematic structural diagram of the third embodiment of the drilling rig parameter monitoring system is shown. In this embodiment, the field bus interfaces 1 and 3 of the data processing unit 100 are used, and its function is to collect the operation data of the drilling rig in real time, and transmit the data to the driller's floor after processing to guide the operator to perform the drilling operation. The data processing unit 100 and multiple data acquisition modules 410 are connected through the RS-485 bus to obtain the operating parameters of the drilling rig in real time, and after calculation, judgment and storage, the operating parameters and status of the drilling rig are sent to the driller's floor through the field bus interface 1 Operating unit 200.
PUM
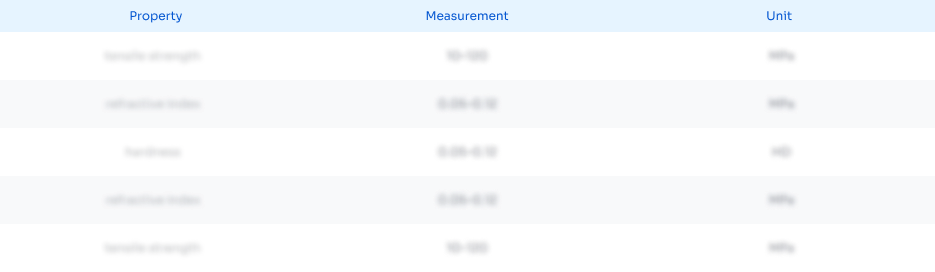
Abstract
Description
Claims
Application Information

- R&D
- Intellectual Property
- Life Sciences
- Materials
- Tech Scout
- Unparalleled Data Quality
- Higher Quality Content
- 60% Fewer Hallucinations
Browse by: Latest US Patents, China's latest patents, Technical Efficacy Thesaurus, Application Domain, Technology Topic, Popular Technical Reports.
© 2025 PatSnap. All rights reserved.Legal|Privacy policy|Modern Slavery Act Transparency Statement|Sitemap|About US| Contact US: help@patsnap.com