A method for manufacturing a combination mold for forming a floor heating pipe groove
A technology of combining molds and floor heating pipes, used in forming tools, manufacturing tools, metal processing equipment, etc., can solve the problems of easy occurrence of wrinkles and difficulty in ensuring the consistency of the size of the floor heating pipe grooves, so as to reduce internal stress and ensure dimensional consistency. , the effect of large molding freedom
- Summary
- Abstract
- Description
- Claims
- Application Information
AI Technical Summary
Problems solved by technology
Method used
Image
Examples
Embodiment 1
[0048] refer to figure 1 , figure 2 and image 3 , the combined mold for forming the floor heating pipe groove of the present embodiment includes an upper mold 2, a forming block 3, a lower mold base 4, a bolt 5 and a compression spring 501, and a U-shaped groove is opened on the lower mold base 4, and the left and right sides of the U-shaped groove Two molding blocks 3 are symmetrically arranged; side through holes 401 are symmetrically arranged on both sides of the lower mold base 4, and the bolts 5 pass through the side through holes 401 to be threadedly connected with the molding blocks 3, and the compression spring 501 is sleeved on the bolts 5, The diameter of compression spring 501 is greater than the inner diameter of side through hole 401, and one end of compression spring 501 is against the head of bolt 5, and the other end of compression spring 501 is against the outside of side through hole 401, and compression spring 501 ends and bolt 5. There is a rubber ring ...
Embodiment 2
[0055] refer to figure 1 , figure 2 and image 3, a floor heating pipe groove forming method using the floor heating pipe groove forming combination mold of embodiment 1, comprising the following steps: 1), installing the mold: installing and fixing the upper mold 2 on the upper tool rest of the bending machine, and placing the lower The mold base 4 is installed and fixed on the lower tool rest of the bending machine, so that the upper mold 2 is directly facing the lower mold base 4 below, that is, the protrusion is located in the middle between the two arc-shaped depressions on the two forming blocks 3 Above; 2), feeding: place the heat conducting layer 1 blank on the top surface 303 of the two molding blocks 3, adjust the position of the heat conducting layer 1 blank, so that the part of the heat conducting layer 1 blank that needs to be stamped out of the floor heating pipe groove 101 is located at the two 3), stamping: the upper die 2 presses down with the upper knife r...
Embodiment 3
[0057] refer to figure 1 , figure 2 and image 3 , The manufacturing method of the floor heating pipe groove forming combination mold of the present embodiment includes the following steps: step (1), blanking; step (2), forging; step (3), rough machining; step (4), punching; Step (5), heat treatment, the heat treatment process in step (5) is quenching and tempering treatment, the hardness of mold after quenching and tempering treatment is HRC40~45, and the hardness of mold after quenching and tempering treatment in the specific present embodiment is HRC40; Step (6 ),finishing.
[0058] Wherein, the structure of the combined mold for forming the floor heating pipe groove is as follows: the combined mold for forming the floor heating pipe groove includes an upper mold 2, a forming block 3, a lower mold base 4, a bolt 5 and a compression spring 501, and the lower mold base 4 is provided with a U-shaped groove, Two molding blocks 3 are symmetrically arranged in the U-shaped gr...
PUM
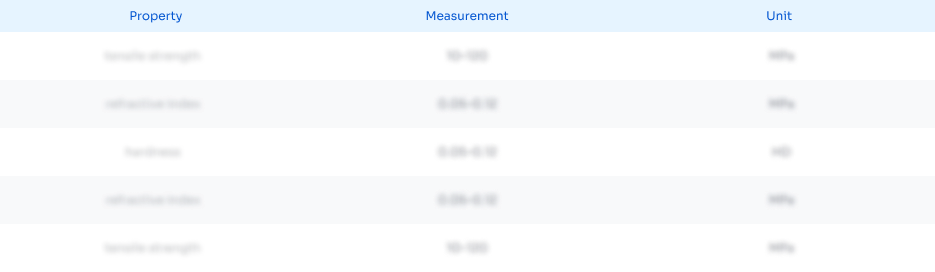
Abstract
Description
Claims
Application Information

- R&D
- Intellectual Property
- Life Sciences
- Materials
- Tech Scout
- Unparalleled Data Quality
- Higher Quality Content
- 60% Fewer Hallucinations
Browse by: Latest US Patents, China's latest patents, Technical Efficacy Thesaurus, Application Domain, Technology Topic, Popular Technical Reports.
© 2025 PatSnap. All rights reserved.Legal|Privacy policy|Modern Slavery Act Transparency Statement|Sitemap|About US| Contact US: help@patsnap.com