Robot and robotic system
A robot and feeder technology, applied in the direction of robots, manipulators, auxiliary devices, etc., can solve the problems of large space and small space, and achieve the effect of restraining space and compact appearance
- Summary
- Abstract
- Description
- Claims
- Application Information
AI Technical Summary
Problems solved by technology
Method used
Image
Examples
Embodiment Construction
[0024] Hereinafter, embodiments of the robot and the robot system disclosed in the present application will be described in detail with reference to the drawings. In addition, this invention is not limited to embodiment shown below.
[0025] In the following, a robot used for arc welding will be described as an example. In addition, the welding torch is described as "welding torch".
[0026] First, the outline of the robot 10 of the embodiment will be described. Figure 1A It is a schematic side view of the robot 10 of the embodiment. In addition, in the following, for convenience of description, it is assumed that the rotational position and posture of the robot 10 are basically at Figure 1A The state shown is the description of the positional relationship of each part in the robot 10 . In addition, sometimes the Figure 1A The state shown is referred to as the "basic posture" of the robot 10 .
[0027] In addition, the installation surface side of the base portion 11 on ...
PUM
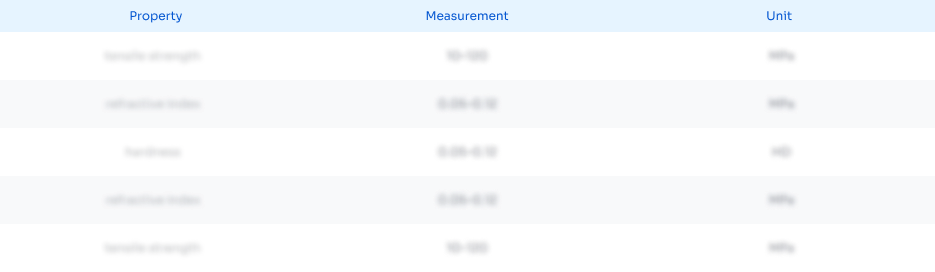
Abstract
Description
Claims
Application Information

- R&D
- Intellectual Property
- Life Sciences
- Materials
- Tech Scout
- Unparalleled Data Quality
- Higher Quality Content
- 60% Fewer Hallucinations
Browse by: Latest US Patents, China's latest patents, Technical Efficacy Thesaurus, Application Domain, Technology Topic, Popular Technical Reports.
© 2025 PatSnap. All rights reserved.Legal|Privacy policy|Modern Slavery Act Transparency Statement|Sitemap|About US| Contact US: help@patsnap.com