Non-contact online detection method for circular degree error and abrasion loss of metal based abrasion wheel and device for achieving method
A roundness error, non-contact technology, applied in the field of grinding, can solve the problems of narrow application range of grinding wheel wear, roundness error of metal-based grinding wheel, etc., and achieve the effect of wide application range, high sensitivity and high detection accuracy
- Summary
- Abstract
- Description
- Claims
- Application Information
AI Technical Summary
Problems solved by technology
Method used
Image
Examples
specific Embodiment approach 1
[0015] Specific implementation mode one: combine figure 1 Describe this embodiment, a non-contact metal-based grinding wheel roundness error and wear amount online detection method described in this embodiment, the method is: the position of the eddy current sensor 1 is fixed, and the eddy current sensor 1 is used to measure the eddy current The distance between the probe of the sensor 1 and the surface of the metal-based grinding wheel 6 is calculated according to the change of the distance to obtain the change of the radius of the metal-based grinding wheel 6, and the radius of the metal-based grinding wheel 6 during the grinding process is obtained according to the change of the radius of the metal-based grinding wheel 6. For the roundness error curve, the wear amount at different positions on the surface of the metal-based grinding wheel 6 is calculated by comparing the changes in the radius of the grinding wheel at different positions before and after grinding.
[0016] T...
specific Embodiment approach 2
[0021] Specific implementation mode two: combination figure 1 Describe this embodiment. This embodiment is a further limitation of the non-contact metal-based grinding wheel roundness error and wear amount online detection method described in Embodiment 1. In this embodiment, the method is specifically: The measuring head of the eddy current sensor 1 is fixed in the radial direction perpendicular to the middle section of the grinding wheel axis of rotation, and the distance between the measuring head of the eddy current sensor 1 and the surface of the metal-based grinding wheel 6 is measured by using the eddy current sensor 1, according to the change of the distance The change of the radius of the metal-based grinding wheel 6 is calculated, and the roundness error curve and the wear amount of the metal-based grinding wheel 6 during the grinding process are obtained according to the change of the radius of the metal-based grinding wheel 6 for one revolution; by comparing the rad...
specific Embodiment approach 3
[0022] Specific implementation mode three: combination figure 1 Describe this embodiment. This embodiment is a further limitation of the non-contact metal-based grinding wheel roundness error and wear amount online detection method described in Embodiment 2. In this embodiment, a photoelectric code disc 4 is used to detect The angular position of each point on the outer circle of the grinding wheel 6 is measured and positioned to obtain the position information of the roundness error curve of the metal base grinding wheel 6 and the wear amount of each point on the grinding wheel surface.
[0023] The photoelectric code disc is installed coaxially with the metal-based grinding wheel. The distance detected by the eddy current sensor is displayed and recorded by the LABVIEW program on the computer, and then the MATLAB program filters, calculates and draws the roundness error curve. The specific position information of the wear point and roundness error is fed back to the machine...
PUM
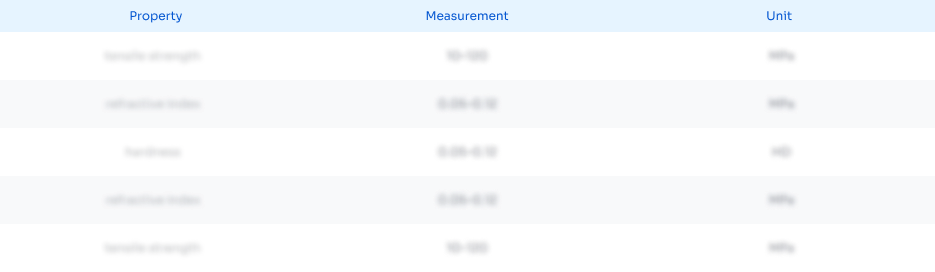
Abstract
Description
Claims
Application Information

- R&D
- Intellectual Property
- Life Sciences
- Materials
- Tech Scout
- Unparalleled Data Quality
- Higher Quality Content
- 60% Fewer Hallucinations
Browse by: Latest US Patents, China's latest patents, Technical Efficacy Thesaurus, Application Domain, Technology Topic, Popular Technical Reports.
© 2025 PatSnap. All rights reserved.Legal|Privacy policy|Modern Slavery Act Transparency Statement|Sitemap|About US| Contact US: help@patsnap.com