A kind of pure epoxy powder coating for electromagnetic wire coating and preparation method thereof
A technology of epoxy powder and magnet wire, which is applied in the direction of powder coating, epoxy resin coating, coating, etc., can solve the problems of cracking of magnet wire and poor flexibility of coating, and achieve good leveling performance, good flexibility, good looking effect
- Summary
- Abstract
- Description
- Claims
- Application Information
AI Technical Summary
Problems solved by technology
Method used
Image
Examples
Embodiment 1
[0034] Epoxy equivalent 1500-1800 epoxy resin 200 parts
[0035] Micronized dicyandiamide 4.5 parts
[0036] Acrylic leveling agent PLP-100 2.4 parts
[0037] Benzoin 2.4 parts
[0038] Barium sulfate 10 parts
[0039] Carbon black 3 parts
[0040] Preparation:
[0041] (1) Weighing epoxy resin, micronized dicyandiamide, leveling agent, benzoin, barium sulfate and carbon black in proportion, placed in a mixing tank, fully mixed and crushed to obtain a mixed premixed material;
[0042] (2) The mixed and premixed materials are sent to the twin-screw extruder for extrusion, and the extrusion temperature is controlled between 130-150°C;
[0043] (3) The extruded material is compressed by a tablet machine, cooled, crushed, sieved, and then packed.
Embodiment 2
[0045] Epoxy equivalent 1450-1600 epoxy resin 200 parts
[0046] Micronized dicyandiamide 5 parts
[0047] Acrylic leveling agent PLP-100 2.2 parts
[0048] Benzoin 2.2 parts
[0049] Silica powder 5 parts
[0050] Carbon black 3 parts
[0051] Preparation:
[0052] (1) Weigh epoxy resin, micronized dicyandiamide, leveling agent, benzoin, silicon micropowder and carbon black in proportion, place in a mixing tank, fully mix and crush to obtain a mixed premixed material;
[0053] (2) The mixed and premixed materials are sent to the twin-screw extruder for extrusion, and the extrusion temperature is controlled between 130-140°C;
[0054] (3) The extruded material is compressed by a tablet machine, cooled, crushed, sieved, and then packed.
Embodiment 3
[0056] Epoxy equivalent 2300-3000 epoxy resin 200 parts
[0057] Micronized dicyandiamide 3 parts
[0058] Acrylic leveling agent PLP-100 3 parts
[0059] Benzoin 2.4 parts
[0060] Titanium dioxide 2 parts
[0061] 2 parts organic red pigment
[0062] Preparation:
[0063] (1) Weigh epoxy resin, micronized dicyandiamide, leveling agent, benzoin, titanium dioxide and organic red pigment in proportion, place them in a mixing tank, fully mix and crush to obtain a mixed premixed material;
[0064] (2) The mixed and premixed materials are sent to the twin-screw extruder for extrusion, and the extrusion temperature is controlled between 150-160°C;
[0065] (3) The extruded material is compressed by a tablet machine, cooled, crushed, sieved, and then packed.
PUM
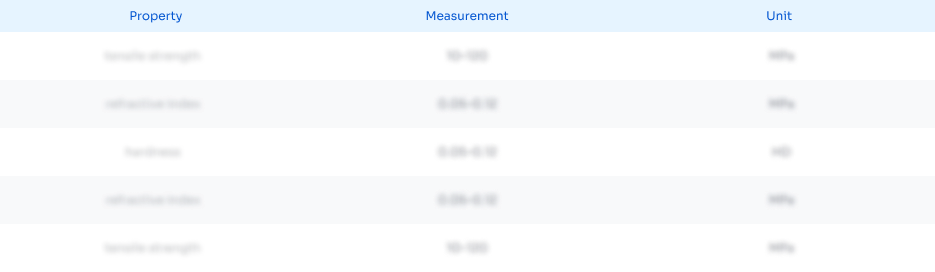
Abstract
Description
Claims
Application Information

- R&D Engineer
- R&D Manager
- IP Professional
- Industry Leading Data Capabilities
- Powerful AI technology
- Patent DNA Extraction
Browse by: Latest US Patents, China's latest patents, Technical Efficacy Thesaurus, Application Domain, Technology Topic, Popular Technical Reports.
© 2024 PatSnap. All rights reserved.Legal|Privacy policy|Modern Slavery Act Transparency Statement|Sitemap|About US| Contact US: help@patsnap.com