A robotic automatic grinding device for large workpieces
A technology for large workpieces and industrial robots, which is applied in the direction of grinding/polishing safety devices, grinding workpiece supports, grinding machines, etc. Safe and guaranteed cleaning effect
- Summary
- Abstract
- Description
- Claims
- Application Information
AI Technical Summary
Problems solved by technology
Method used
Image
Examples
specific Embodiment approach 1
[0017] Specific implementation mode one: combine Figure 1 to Figure 5 Describe this embodiment, this embodiment comprises industrial robot 1, grinding device 2, mobile platform 3, lead screw 4, track 5 and base 6, the tail of industrial robot 1 is fixed on the mobile platform 3 by base 6, mobile platform 3 is threadedly connected with the lead screw 4, the lead screw 4 is driven by the driving motor, the mobile platform 3 is slidably connected with the rail 5, the length direction of the guide rail 5 is parallel to the length direction of the workpiece fixture (not shown), and the grinding device 2 is installed in the industrial The end of the robot 1; the grinding device 2 includes a buffer assembly 21, a vacuum chuck 22, grinding paper 23, a resin cover 24, an annular felt 25 and two negative pressure adsorption devices 26, and the buffer assembly 21 includes an upper contact plate 211, a retaining spring 212, buffer spring 213, drive motor 214, lower contact plate 215 and ...
specific Embodiment approach 2
[0018] Specific implementation mode two: combination figure 2 and image 3 The present embodiment will be described. The material of the vacuum chuck 22 of the present embodiment is cemented carbide. The rigidity of cemented carbide is good, which can maintain a large enough contact force between the vacuum chuck 22 and the workpiece 7 . Other components and connections are the same as those in the first embodiment.
specific Embodiment approach 3
[0019] Specific implementation mode three: combination Figure 5 To describe this embodiment, the lower end surface of the vacuum chuck 22 of this embodiment is provided with an annular groove 222 . By adopting a suction cup with an annular groove, it is easy to form a negative pressure on the surface of the suction cup, thereby realizing the adsorption of the grinding paper. Other compositions and connections are the same as those in Embodiment 1 or 2.
PUM
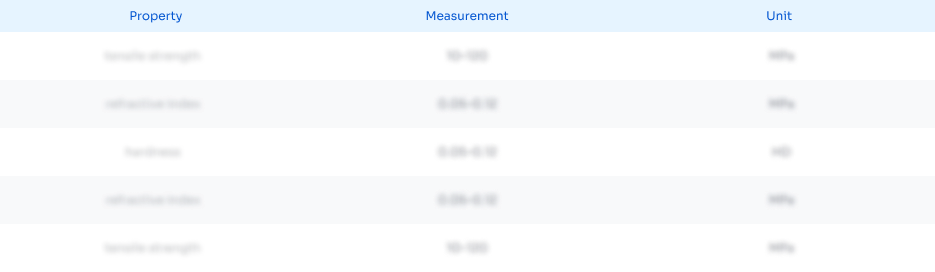
Abstract
Description
Claims
Application Information

- R&D
- Intellectual Property
- Life Sciences
- Materials
- Tech Scout
- Unparalleled Data Quality
- Higher Quality Content
- 60% Fewer Hallucinations
Browse by: Latest US Patents, China's latest patents, Technical Efficacy Thesaurus, Application Domain, Technology Topic, Popular Technical Reports.
© 2025 PatSnap. All rights reserved.Legal|Privacy policy|Modern Slavery Act Transparency Statement|Sitemap|About US| Contact US: help@patsnap.com