Double air chamber heated urea catalytic hydrolysis reactor and method
A urea catalytic hydrolysis and reactor technology, which is applied in the field of urea catalytic hydrolysis reactor heated by double chambers, can solve the problems of difficult cleaning, high urea purity requirements, and no consideration of impurity treatment, etc.
- Summary
- Abstract
- Description
- Claims
- Application Information
AI Technical Summary
Problems solved by technology
Method used
Image
Examples
Embodiment 1
[0031] Such as figure 1 As shown, the urea catalytic hydrolysis reactor heated by double chambers provided by the present invention includes a blowdown chamber 1 ; a baffle plate 2 ; and a reaction chamber 3 . In this embodiment, the volume of the urea catalytic hydrolysis reactor is 5.9 cubic meters, 1400mm high, and the height of the baffle plate is 980mm, because the liquid level inside the reactor will be half of the height of the reactor, so the height of the baffle plate should be high half the height of the reactor. U-shaped heating coils are installed at the bottoms of the sewage chamber 1 and the reaction chamber 3, and the liquid level in the reactor should be higher than the U-shaped heating coils at this time.
[0032] Step 1: Add 25% (calculated by volume) desalted water into the empty reactor through the urea solution inlet N1 into the reaction chamber 3 to make the liquid level reach 350 mm.
[0033] Step 2: A certain amount of catalyst dissolved in urea solut...
PUM
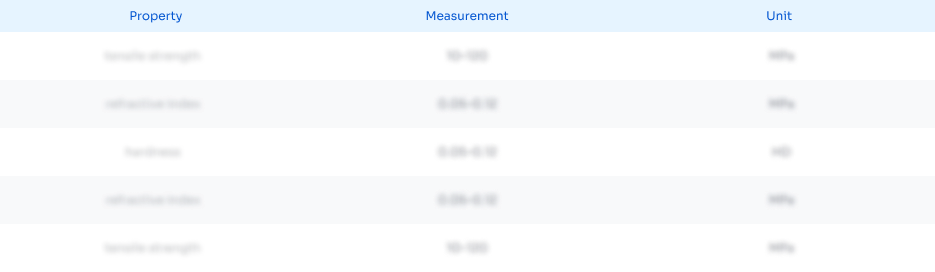
Abstract
Description
Claims
Application Information

- R&D
- Intellectual Property
- Life Sciences
- Materials
- Tech Scout
- Unparalleled Data Quality
- Higher Quality Content
- 60% Fewer Hallucinations
Browse by: Latest US Patents, China's latest patents, Technical Efficacy Thesaurus, Application Domain, Technology Topic, Popular Technical Reports.
© 2025 PatSnap. All rights reserved.Legal|Privacy policy|Modern Slavery Act Transparency Statement|Sitemap|About US| Contact US: help@patsnap.com