Method of controlling single-joint assisting exoskeleton sliding mode
A single-joint, exoskeleton technology, which can be applied to devices that can be operated by the disabled, medical science, prostheses, etc., and can solve immaturity problems
- Summary
- Abstract
- Description
- Claims
- Application Information
AI Technical Summary
Problems solved by technology
Method used
Image
Examples
Embodiment Construction
[0093] The present invention will be further described in conjunction with the accompanying drawings and embodiments.
[0094] Such as figure 1 As shown, a single-joint power-assisted exoskeleton includes: a hydraulic cylinder 1, a joint rotary encoder 2, a force sensor 3, a thigh rod 4, a calf rod 5, a bandage 6, a first pressure sensor 7, and a second pressure sensor 8 , an electro-hydraulic servo valve (not shown in the figure), a servo amplifier plate (not shown in the figure), a real-time controller (not shown in the figure); the thigh rod 4 and the calf rod 5 are connected by a hinge, A joint rotary encoder 2 is arranged at the hinge; one end of the hydraulic cylinder 1 is hinged with the thigh rod 4, and the other end is hinged with the calf rod 5; the first pressure sensor 7 is fixedly installed at one end of the hydraulic cylinder 1, and the second pressure sensor 8 It is fixedly installed on the other end of the hydraulic cylinder 1 ; the force sensor 3 is arranged ...
PUM
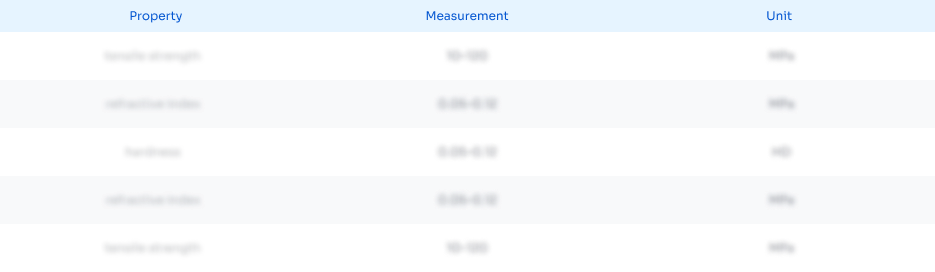
Abstract
Description
Claims
Application Information

- R&D
- Intellectual Property
- Life Sciences
- Materials
- Tech Scout
- Unparalleled Data Quality
- Higher Quality Content
- 60% Fewer Hallucinations
Browse by: Latest US Patents, China's latest patents, Technical Efficacy Thesaurus, Application Domain, Technology Topic, Popular Technical Reports.
© 2025 PatSnap. All rights reserved.Legal|Privacy policy|Modern Slavery Act Transparency Statement|Sitemap|About US| Contact US: help@patsnap.com