Multilane laser light plane calibration method based on binocular vision
A multi-line laser, binocular vision technology, applied in the field of image processing and visual measurement, can solve the problems of small number of calibration points, positioning accuracy susceptible to camera distortion, difficult to obtain calibration accuracy, etc., to achieve high calibration accuracy and improve practicality. sexual effect
- Summary
- Abstract
- Description
- Claims
- Application Information
AI Technical Summary
Problems solved by technology
Method used
Image
Examples
Embodiment Construction
[0055] Below in conjunction with accompanying drawing, technical scheme of the present invention is described in further detail:
[0056] figure 1 Shown is the multi-laser line scanning device used in the implementation of the present invention, which consists of left and right eye cameras and a multi-line laser emitter. Both the left and right eye cameras use the DMK23U445 industrial camera from TheImagingSource Company, the sensor is 1 / 3"CCD, the output mode is USB3.0, and the lens uses ComputarM0814-MP2 megapixel fixed-focus lens. The two cameras are rigidly connected by the skeleton, and the left and right eye cameras The angle between the optical axes is about 40°, and the baseline distance is about 25cm. The multi-line laser is located in the middle of the two cameras and emits 5 parallel beams.
[0057] Such as figure 2 Shown is a schematic diagram of the target of the present invention. There are 5 rows and 6 columns of circular marking points distributed on the tar...
PUM
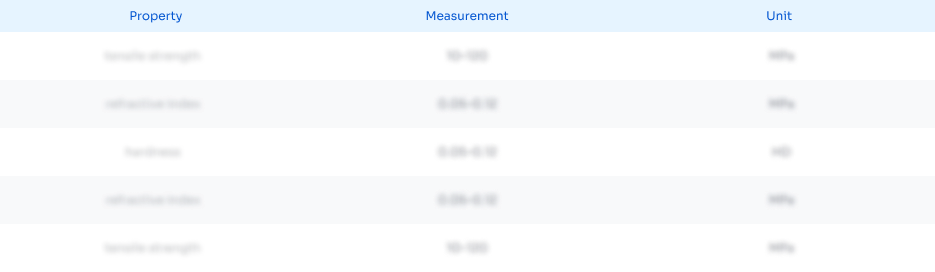
Abstract
Description
Claims
Application Information

- Generate Ideas
- Intellectual Property
- Life Sciences
- Materials
- Tech Scout
- Unparalleled Data Quality
- Higher Quality Content
- 60% Fewer Hallucinations
Browse by: Latest US Patents, China's latest patents, Technical Efficacy Thesaurus, Application Domain, Technology Topic, Popular Technical Reports.
© 2025 PatSnap. All rights reserved.Legal|Privacy policy|Modern Slavery Act Transparency Statement|Sitemap|About US| Contact US: help@patsnap.com