Cement expansion agent suitable for high temperature environment and preparation method thereof
A high-temperature environment, expansion agent technology, applied in the field of composite cement expansion agent and its preparation, to achieve the effect of preventing gas channeling, no effect on thickening time and compressive strength, and moderate onset time
- Summary
- Abstract
- Description
- Claims
- Application Information
AI Technical Summary
Problems solved by technology
Method used
Image
Examples
Embodiment 1
[0040] 85 kg of dead-burned MgO (MgO content ≥ 98.5%) raw materials obtained by calcining and sintering the screened magnesite at a high temperature of 2850°C, fumed silica (SiO 2 Content ≥ 94%) 10kg, calcareous raw material hemihydrate gypsum 5.0kg, expansion inhibitor sodium citrate 0.01kg, add ball mill to grind in proportion, mix, and then sieve.
[0041] Among them, the grinding fineness is controlled at 0.010-0.075mm, the residue on a 325-mesh sieve is less than 7.5%, and the activity is measured for 109 minutes.
[0042] The high-temperature expansion agent for oil well cement of the present invention is obtained after metering and packaging.
Embodiment 2
[0044] 92 kg of dead-burned MgO (MgO content ≥ 97.5%) raw materials formed by sintering and sintering magnesite at a high temperature of 2800° C., fumed silica (SiO content ≥ 94% ) 4.5kg, calcareous raw material hemihydrate gypsum 3.5kg, expansion inhibitor sodium citrate 0.02kg, add ball mill grinding in proportion, mix, then sieve.
[0045] The grinding fineness is controlled to be 0.010-0.075mm, the 325-mesh sieve balance is less than 5.5%, and the activity is measured for 86 minutes.
[0046] The high-temperature expansion agent for oil well cement of the present invention is obtained after metering and packaging.
Embodiment 3
[0048] 96 kg of dead-burned MgO (MgO content ≥ 96.5%) raw materials formed by calcining and sintering the screened magnesite at a sintering temperature of 2700° C., fumed silica (SiO2 content ≥ 94% ) 1.5kg, calcareous raw material hemihydrate gypsum 2.5kg, expansion inhibitor sodium citrate 0.01kg, add ball mill grinding in proportion, mix, and then sieve.
[0049] Among them, the grinding fineness is controlled to be 0.010-0.075mm, and the particle size is preferably controlled to be less than 3.5% on a 325-mesh sieve, and the control activity is measured for 71 minutes.
[0050] The high-temperature expansion agent for oil well cement of the present invention is obtained after metering and packaging.
PUM
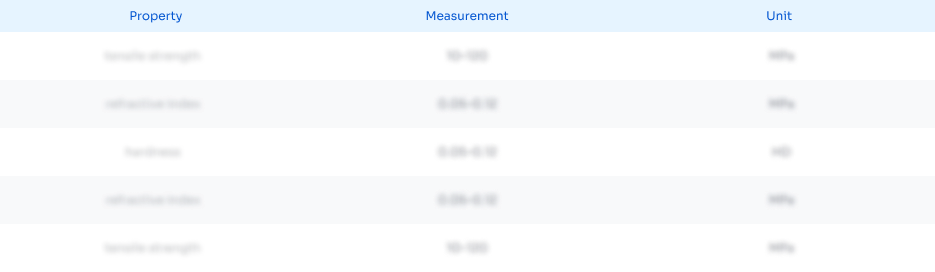
Abstract
Description
Claims
Application Information

- R&D Engineer
- R&D Manager
- IP Professional
- Industry Leading Data Capabilities
- Powerful AI technology
- Patent DNA Extraction
Browse by: Latest US Patents, China's latest patents, Technical Efficacy Thesaurus, Application Domain, Technology Topic, Popular Technical Reports.
© 2024 PatSnap. All rights reserved.Legal|Privacy policy|Modern Slavery Act Transparency Statement|Sitemap|About US| Contact US: help@patsnap.com