Soft and elastic joint based on Achimedean spiral elastomers
A technology of Archimedes spiral and elastic body, which is applied in the direction of manipulators, manufacturing tools, joints, etc., can solve the problems of large space occupied by joints, damage to robots and human bodies, and loose structures, and achieve precise transmission, compact structure, and small size. variable effect
- Summary
- Abstract
- Description
- Claims
- Application Information
AI Technical Summary
Problems solved by technology
Method used
Image
Examples
Embodiment 1
[0025] Such as Figure 1-2 As shown, a flexible elastic joint based on Archimedes spiral elastic body involved in the present invention includes input shaft 1, first one-way bearing 2, elastic body one 3, elastic body two 4, second one-way bearing 5. Long pin one 6, long pin two 7, sleeve 8, output shaft 9 and flange 10.
[0026] Such as image 3 As shown, one end of the input shaft 1 is provided with a keyway for connecting the driving unit such as a motor or a reducer, and the other end is provided with two symmetrical long keyways for connecting the first one-way bearing 2, the elastic body 3, the elastic Body two 4 and the second one-way bearing 5 have a groove respectively on the left and right sides of the displacement long keyway, which is used for the positioning of the jump spring.
[0027] Such as Figure 4 As shown, elastic body 1 3 and elastic body 2 4 are made of spring steel and other elastic materials, and there are two key grooves on the inner hole wall, whi...
Embodiment 2
[0031] The test uses a motor as the power input end of the flexible joint of the present invention, an angular velocity sensor is installed on the output shaft 9, and then the motor is turned on to collect angular velocity data, and the collected data can be sorted to obtain Figure 6 . Depend on Figure 6 It can be obtained that the output shaft does not rotate immediately after the motor is energized, but starts to rotate slowly after about 0.2s, and the speed stabilizes after about 1.2s. The flexible elastic joint of the elastomer has good flexibility output.
PUM
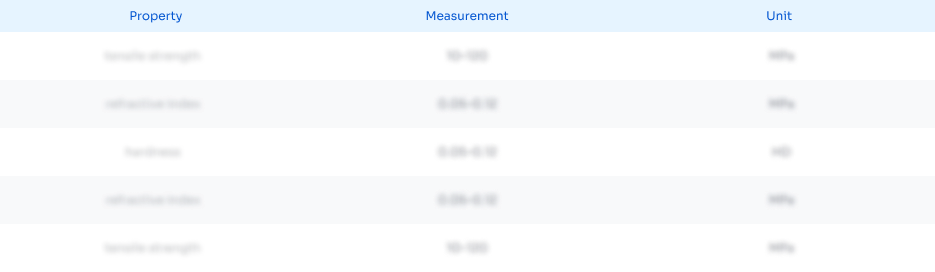
Abstract
Description
Claims
Application Information

- Generate Ideas
- Intellectual Property
- Life Sciences
- Materials
- Tech Scout
- Unparalleled Data Quality
- Higher Quality Content
- 60% Fewer Hallucinations
Browse by: Latest US Patents, China's latest patents, Technical Efficacy Thesaurus, Application Domain, Technology Topic, Popular Technical Reports.
© 2025 PatSnap. All rights reserved.Legal|Privacy policy|Modern Slavery Act Transparency Statement|Sitemap|About US| Contact US: help@patsnap.com