Machining method for helicopter fairing supporting piece
A processing method and fairing technology, applied in metal processing equipment, metal processing mechanical parts, supports, etc., can solve problems such as clamping difficulties, and achieve the effect of solving clamping problems and saving tooling and CNC machine tool resources.
- Summary
- Abstract
- Description
- Claims
- Application Information
AI Technical Summary
Problems solved by technology
Method used
Image
Examples
Embodiment Construction
[0014] The installation and working methods of the present invention will be described below in conjunction with the accompanying drawings.
[0015] first step, such as figure 1 As shown, part 3 is a conical tubular structure, which needs to be turned and milled on its inner and outer surfaces, and clamped. The part 3 is fixed and clamped by the positioning fixture and the intermediate pressure plate 2, so as to ensure that the outer surface of the blank and the inner surface of the intermediate pressure plate 2 are more than 2 The area can be processed, except for the area of the intermediate platen 2 and the installation position 1 of the positioning fixture for rough turning, leave a margin of 1mm;
[0016] The second step is to install the four side splints 4, remove the middle pressure plate 2, and fix the part 3 from the outside, such as figure 2 As shown, the remaining unprocessed area in the first step of rough turning, finishing turning and finishing milling inclu...
PUM
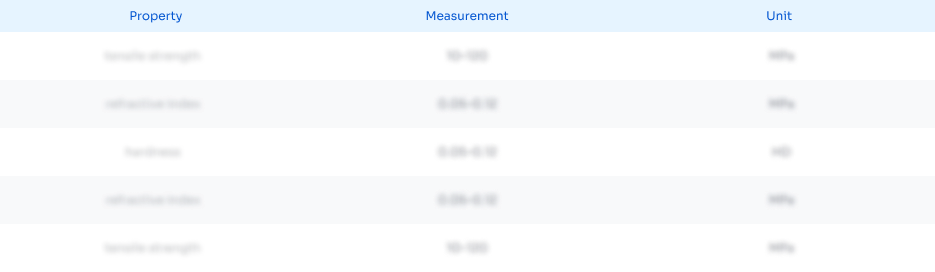
Abstract
Description
Claims
Application Information

- R&D Engineer
- R&D Manager
- IP Professional
- Industry Leading Data Capabilities
- Powerful AI technology
- Patent DNA Extraction
Browse by: Latest US Patents, China's latest patents, Technical Efficacy Thesaurus, Application Domain, Technology Topic, Popular Technical Reports.
© 2024 PatSnap. All rights reserved.Legal|Privacy policy|Modern Slavery Act Transparency Statement|Sitemap|About US| Contact US: help@patsnap.com