Electric main shaft system modeling method taking features of combination portions into consideration
A system modeling and combination technology, applied in the general control system, control/regulation system, electrical program control, etc.
- Summary
- Abstract
- Description
- Claims
- Application Information
AI Technical Summary
Problems solved by technology
Method used
Image
Examples
Embodiment Construction
[0017] The present invention implements a motorized spindle system modeling method considering the characteristics of joints. The implementation of the present invention will be described in detail below in conjunction with the accompanying drawings.
[0018] figure 1 It is a schematic diagram of the finite element model of the electric spindle system. As shown in the figure, the main shaft-tool holder-tool shaft segment is modeled by Timoshenko beam elements for finite element modeling. The stiffness of the spindle-bearing joint and the stiffness of the bearing are in a series relationship, and the support stiffness can be calculated according to the series formula. The main shaft-knife handle-tool joint is simplified as a distributed spring, and the spring interval is consistent with the length of the shaft segment unit. Step (1), identify the stiffness of the joint of the motorized spindle system
[0019] 1.1 Frequency response function method
[0020] The frequency res...
PUM
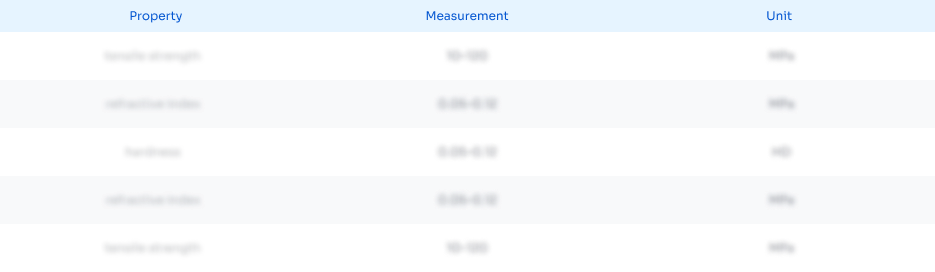
Abstract
Description
Claims
Application Information

- R&D
- Intellectual Property
- Life Sciences
- Materials
- Tech Scout
- Unparalleled Data Quality
- Higher Quality Content
- 60% Fewer Hallucinations
Browse by: Latest US Patents, China's latest patents, Technical Efficacy Thesaurus, Application Domain, Technology Topic, Popular Technical Reports.
© 2025 PatSnap. All rights reserved.Legal|Privacy policy|Modern Slavery Act Transparency Statement|Sitemap|About US| Contact US: help@patsnap.com