Carrier band forming device and method
A molding device and carrier tape technology, which is applied to belts, other household appliances, household appliances, etc., can solve the problems of inability to manufacture carrier tapes, increased manufacturing costs of carrier tapes, and impossibility, so as to save the manufacturing cost of carrier tapes and save manufacturing The effect of reducing cost and reducing processing difficulty
- Summary
- Abstract
- Description
- Claims
- Application Information
AI Technical Summary
Problems solved by technology
Method used
Image
Examples
Embodiment 1
[0042] This embodiment describes a carrier tape forming device for making a sheet into a carrier tape; its structure is as follows figure 1 Shown; including frame and gas input unit, as well as molding upper mold 1, molding lower mold 3 and clamping unit 2.
[0043] Wherein, forming lower mold 3 is positioned at the lower side of clamping unit 2, as figure 2 As shown; the clamping unit 2 is connected to the frame; the forming lower mold 3 is connected to the frame through the lower mold driving unit to realize that the forming lower mold 3 moves toward the clamping unit 2 and moves away from the clamping unit 2, thereby realizing the clamping unit 2 and the distance between the forming lower die 3 is adjusted. The clamping unit 2 and the lower forming die 3 are used to clamp the sheet, and the positioning of the sheet can be realized by adjusting the distance between the clamping unit 2 and the lower forming die 3 .
[0044] Such as image 3 As shown, the forming upper mol...
Embodiment 2
[0055] The difference between the carrier tape forming device of this embodiment and Embodiment 1 is that: in the carrier tape forming device of this embodiment, the forming lower mold is connected to the frame; the clamping unit is connected to the frame through the clamping drive unit to move the clamping unit to Realize the adjustment of the distance between the clamping unit and the forming lower mold. The rest of the structure of this embodiment is the same as that of Embodiment 1.
Embodiment 3
[0057] This embodiment describes a carrier tape forming method, which is used to make a sheet into a carrier tape, and its working process is as follows Figure 7 shown; includes the following steps:
[0058] In the first step, the sheet is placed on the side of the forming lower die with the lower die hole, and the clamping unit is used to clamp the sheet together with the forming lower die;
[0059] In the second step, the forming upper mold moves toward the forming lower mold until the forming cylinder with the forming upper mold enters the lower mold hole opened by the forming lower mold, and the sheet is positioned at the lower mold hole during the forming cylinder enters the lower mold hole. The part of the die hole is pressed into the lower die hole by the forming cylinder to form the initial cavity; since the gap between the forming cylinder and the lower die hole is greater than the thickness of the sheet, the initial cavity is respectively connected to the forming cy...
PUM
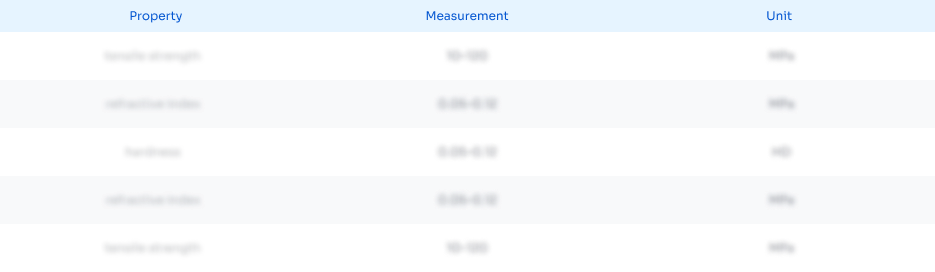
Abstract
Description
Claims
Application Information

- R&D
- Intellectual Property
- Life Sciences
- Materials
- Tech Scout
- Unparalleled Data Quality
- Higher Quality Content
- 60% Fewer Hallucinations
Browse by: Latest US Patents, China's latest patents, Technical Efficacy Thesaurus, Application Domain, Technology Topic, Popular Technical Reports.
© 2025 PatSnap. All rights reserved.Legal|Privacy policy|Modern Slavery Act Transparency Statement|Sitemap|About US| Contact US: help@patsnap.com