Multi-return-stroke gas-steam boiler
A gas steam, multi-return technology, applied in steam boilers, fire tube steam boilers, steam generation and other directions, can solve the problems of low gas combustion efficiency, short flue gas flow, slow combustion speed, etc., to improve utilization, reduce Flame temperature, improved combustion effect
- Summary
- Abstract
- Description
- Claims
- Application Information
AI Technical Summary
Problems solved by technology
Method used
Image
Examples
Embodiment Construction
[0010] Such as figure 1 As shown, the present invention discloses a multi-return gas-fired steam boiler, comprising a furnace chamber 1, a furnace chamber 2 is provided at the bottom of the furnace chamber 1, a burner 3 is connected to the front end of the furnace chamber 2, and the furnace chamber 2 The top of the furnace has a steam outlet 13, and the end of the furnace 2 has a combustion chamber 4, and the combustion chamber 4 has an explosion-proof door 17, and the upper part of the combustion chamber 4 communicates with the second return smoke pipe 5, The other end of the two-pass smoke pipe 5 communicates with the front smoke box 6 at the front end of the furnace 2, and the front smoke box 6 communicates with the rear smoke box 8 at the end of the furnace 2 through the three-pass smoke pipe 7, and the burner 3. After the injected gas is mixed with air, it burns in the furnace 2, and the high-temperature flue gas formed by the combustion flows through the back-burning ch...
PUM
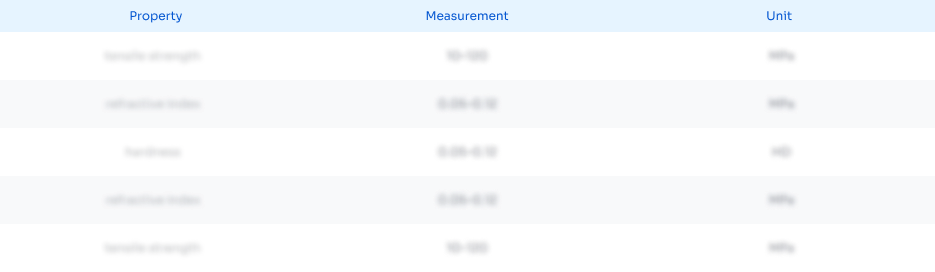
Abstract
Description
Claims
Application Information

- R&D
- Intellectual Property
- Life Sciences
- Materials
- Tech Scout
- Unparalleled Data Quality
- Higher Quality Content
- 60% Fewer Hallucinations
Browse by: Latest US Patents, China's latest patents, Technical Efficacy Thesaurus, Application Domain, Technology Topic, Popular Technical Reports.
© 2025 PatSnap. All rights reserved.Legal|Privacy policy|Modern Slavery Act Transparency Statement|Sitemap|About US| Contact US: help@patsnap.com