A preparation method of antistatic nylon 6 composite material and the composite material
A composite material and antistatic technology, applied in the field of functional composite materials, can solve the problems that affect the performance of nylon 6 composite materials, the mechanical properties of composite materials have not been reported, and the electrical conductivity of composite materials is limited. Mechanical properties, avoid water vapor contact, improve the effect of mechanical properties
- Summary
- Abstract
- Description
- Claims
- Application Information
AI Technical Summary
Problems solved by technology
Method used
Image
Examples
preparation example Construction
[0025] The preparation method of antistatic nylon 6 composite material of the present invention specifically comprises the steps:
[0026] (1) Heat and dry the conductive filler in a vacuum oven at 120-200°C for 4-8 hours;
[0027] (2) Heat the caprolactam monomer in the reaction vessel to 110-130°C to melt the material, add the initiator after vacuum dehydration for 0.5-1 hour, and continue the vacuum dehydration for 0.5-1 hour; remove the vacuum, add conductive filler, and raise The temperature of the reaction solution is 130-150°C, high-speed stirring, dispersion and emulsification for 0.5-1 hour, and then vacuum dehydration for 0.5-1 hour. The vacuum degree during vacuum dehydration is less than or equal to 10 -2 Pa; High-speed stirring, dispersing and emulsifying uses a high-speed homogenizer with a speed of 500-4000rpm.
[0028] (3) After releasing the vacuum, add the catalyst to disperse for 1-8 minutes, use the vacuum-assisted resin molding method to pump the reactio...
Embodiment 1
[0036] Dry natural graphite in a vacuum oven at 120°C for 8 hours, then add 100 parts by mass of caprolactam monomer into a 1L reactor, heat up to 110°C to melt, add 0.1 part by mass of sodium methoxide after vacuum dehydration for 0.5 hours, and continue vacuum dehydration for 0.5 hours (vacuum less than 10 -2 Pa), then add 1 mass part of natural graphite, use a high-speed homogenizer to disperse and emulsify for 0.5 hours (rotating speed 500rpm) and heat to 140°C, vacuum dehydrate for 1 hour, add 0.3 mass parts of toluene 2,4 diisocyanate after removing the vacuum, After stirring for 8 minutes, quickly use the vacuum-assisted resin transfer molding process to pump the reaction solution into a flat mold that has been preheated to 150°C (vacuum degree 0.08MPa), demould after 0.5 hours, and obtain an antistatic nylon 6 compound after post-processing Material. The typical properties of the composite materials are shown in Table 1.
Embodiment 2
[0038] Dry natural graphite in a vacuum oven at 120°C for 8 hours, then add 100 parts by mass of caprolactam monomer into a 1L reactor, heat up to 110°C to melt, add 0.3 parts by mass of sodium methoxide after vacuum dehydration for 1 hour, and continue vacuum dehydration for 0.5 hours (vacuum degree 10 -2 Pa), then add 10 parts by mass of natural graphite, use a high-speed homogenizer to disperse and emulsify for 1 hour (rotational speed 2000rpm) and heat to 140°C, vacuum dehydrate for 0.5 hours, and add 0.6 parts by mass of tetrahydrofuran modified toluene after removing the vacuum 2,4 Diisocyanate, after stirring for 5 minutes, the reaction solution was pumped and injected into the flat mold preheated to 170°C (vacuum degree 0.03MPa) by vacuum-assisted resin transfer molding process, and demolded after 0.5 hours, and the anti- Electrostatic nylon 6 composite. The typical properties of the composite materials are shown in Table 1.
PUM
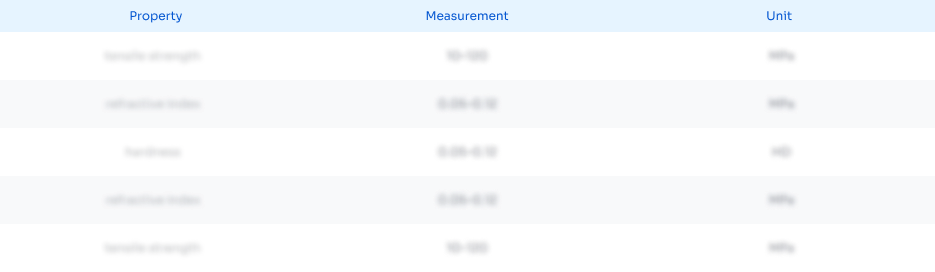
Abstract
Description
Claims
Application Information

- R&D
- Intellectual Property
- Life Sciences
- Materials
- Tech Scout
- Unparalleled Data Quality
- Higher Quality Content
- 60% Fewer Hallucinations
Browse by: Latest US Patents, China's latest patents, Technical Efficacy Thesaurus, Application Domain, Technology Topic, Popular Technical Reports.
© 2025 PatSnap. All rights reserved.Legal|Privacy policy|Modern Slavery Act Transparency Statement|Sitemap|About US| Contact US: help@patsnap.com