Fully-automatic pipe end molding machine
A forming machine, fully automatic technology, applied in the field of fully automatic pipe end forming machine, can solve the problems of inconvenient fully automatic production and promotion, difficult processing and positioning, high production cost, etc., and achieve the effect of fast processing speed, convenient operation and high precision
- Summary
- Abstract
- Description
- Claims
- Application Information
AI Technical Summary
Problems solved by technology
Method used
Image
Examples
Embodiment
[0023] Embodiment: A fully automatic pipe end forming machine
[0024] refer to Figure 1 to Figure 5 As shown, a fully automatic pipe end forming machine includes a stand 1, a fixed mount 3 is installed on the upper surface of the stand 1, and a retractable oil cylinder 2 is installed on the left end of the fixed mount 3, and the retracted oil cylinder 2 The right end of the feeder is connected with a shrinking die head 4, the front surface of the fixed frame 3 is provided with a fixed plate 7, the feeding device A5 and the feeding device B6 are installed on the fixed plate 7, and the right end of the feeding device B6 is connected with a Slider 11, said slider 11 is installed in the middle end of fixed frame 3, and upper mold clamp 8 is installed in the middle of feeding device A5 and feeding device B6, and the top is fixed on the fixed frame 3, and lower mold clamp 9 is installed in the said Just below the upper mold clamp 8, the bottom end is connected with the lower mold...
PUM
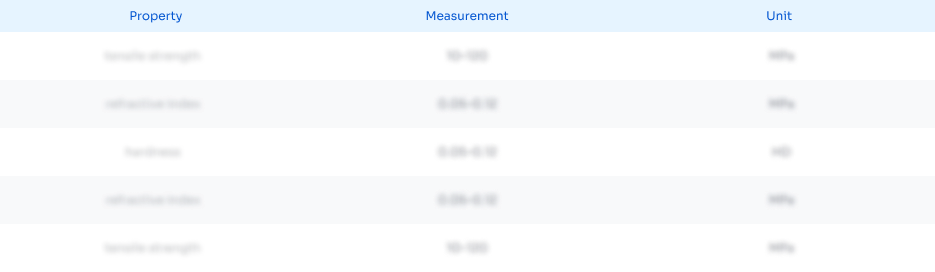
Abstract
Description
Claims
Application Information

- R&D Engineer
- R&D Manager
- IP Professional
- Industry Leading Data Capabilities
- Powerful AI technology
- Patent DNA Extraction
Browse by: Latest US Patents, China's latest patents, Technical Efficacy Thesaurus, Application Domain, Technology Topic, Popular Technical Reports.
© 2024 PatSnap. All rights reserved.Legal|Privacy policy|Modern Slavery Act Transparency Statement|Sitemap|About US| Contact US: help@patsnap.com