Adhesive composition
A pressure-sensitive adhesive, acrylic pressure-sensitive adhesive technology, applied in the direction of adhesive types, ester copolymer adhesives, adhesives, etc., can solve the problems of yield defects, short pot life, etc., to shorten the curing time effect of time
- Summary
- Abstract
- Description
- Claims
- Application Information
AI Technical Summary
Problems solved by technology
Method used
Image
Examples
preparation Embodiment 1
[0117] Preparation Example 1. Preparation of acrylic pressure-sensitive adhesive resin A
[0118] In a 2L reactor in which nitrogen is refluxed and equipped with a cooling device to facilitate temperature control, the weight ratio of 84.1:0.9:15 (EHA:N-ma:HEA) is poured into ethylhexyl acrylate (EHA), N- Hydroxymethylacrylamide (N-ma) and Hydroxyethyl Acrylate (HEA). Subsequently, 149.1 parts by weight of ethyl acetate (EAc) was poured therein as a solvent, and purged with nitrogen for 60 minutes to remove oxygen. With the temperature maintained at 67°C, 0.04 parts by weight of azobisisobutyronitrile (AIBN) was poured therein as a reaction initiator, and the mixture was reacted for 3 hours. The reaction product was diluted with ethyl acetate (EAc) to prepare acrylic pressure-sensitive adhesive resin A.
preparation Embodiment 2
[0119] Preparation Example 2. Preparation of acrylic pressure-sensitive adhesive resin B
[0120] In a 2L reactor in which nitrogen is refluxed and equipped with a cooling device to facilitate temperature control, 85 parts by weight of n-ethylhexyl acrylate (EHA) and 15 parts by weight of hydroxyethyl acrylate (HEA) are poured. Subsequently, 149.1 parts by weight of ethyl acetate (EAc) was poured therein as a solvent, and purged with nitrogen for 60 minutes to remove oxygen. With the temperature maintained at 67°C, 0.04 parts by weight of azobisisobutyronitrile (AIBN) was poured therein as a reaction initiator, and the mixture was reacted for 3 hours. The reaction product was diluted with ethyl acetate (EAc) to prepare an acrylic pressure-sensitive adhesive resin B having a solid concentration of 30% and a molecular weight of 700,000.
[0121] Preparation of pressure-sensitive adhesive composition and protective film
Embodiment 1
[0123] The acrylic pressure-sensitive adhesive resin A obtained in Preparation Example 1 was used. With respect to 100 parts by weight of the pressure-sensitive adhesive resin, a crosslinking agent (wherein, hexamethylene diisocyanate and isophorone diisocyanate are each at 8 : 2), 7 parts by weight of acetylacetone and 0.01 parts by weight of K-KAT 5218 (aluminum chelate catalyst, King Industry Company) to prepare a pressure-sensitive adhesive composition.
[0124] The pressure-sensitive adhesive composition was coated on one side of a polyethylene terephthalate (PET) film (thickness: 50 μm), and treated at 120° C. for 2 minutes to form a coating having a thickness of 20 μm. The transparent pressure-sensitive adhesive layer of the cloth film to prepare a protective film.
PUM
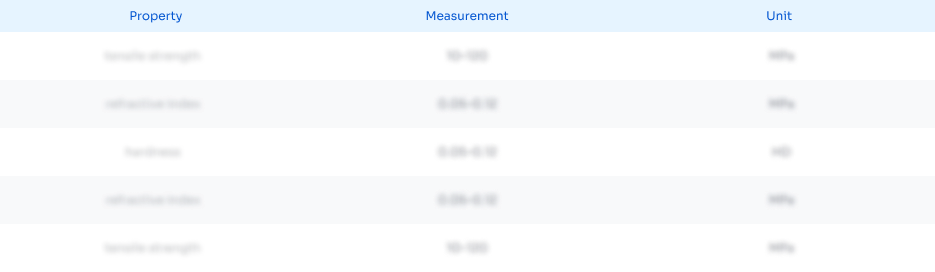
Abstract
Description
Claims
Application Information

- Generate Ideas
- Intellectual Property
- Life Sciences
- Materials
- Tech Scout
- Unparalleled Data Quality
- Higher Quality Content
- 60% Fewer Hallucinations
Browse by: Latest US Patents, China's latest patents, Technical Efficacy Thesaurus, Application Domain, Technology Topic, Popular Technical Reports.
© 2025 PatSnap. All rights reserved.Legal|Privacy policy|Modern Slavery Act Transparency Statement|Sitemap|About US| Contact US: help@patsnap.com