Method of Determining the Initial Position of the Rotor
A technology of rotor position and rotor, applied in the direction of electronic commutator, control electromechanical transmission device, electronic commutation motor control, etc., can solve problems such as sensor failure
- Summary
- Abstract
- Description
- Claims
- Application Information
AI Technical Summary
Problems solved by technology
Method used
Image
Examples
Embodiment Construction
[0017] Various example embodiments will now be described more fully with reference to the accompanying drawings that illustrate some example embodiments.
[0018] Accordingly, while the exemplary embodiments are capable of various changes and alternative forms, the embodiments of the present invention are shown in the drawings by way of example and will be described herein in detail. It should be understood, however, that there is no intention to limit example embodiments to the particular forms disclosed, but on the contrary, example embodiments are to cover all modifications, equivalents, and alternatives falling within the scope of the claims. Like reference numerals refer to like elements throughout the description of the figures.
[0019] It will be understood that although the terms first, second etc. may be used herein to describe various elements, these elements should not be limited by these terms. These terms are only used to distinguish one element from another. F...
PUM
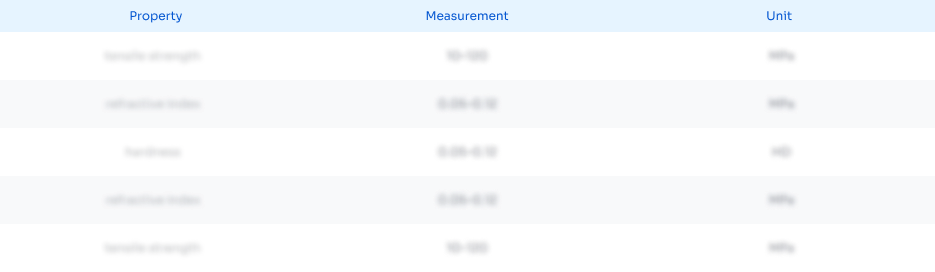
Abstract
Description
Claims
Application Information

- R&D
- Intellectual Property
- Life Sciences
- Materials
- Tech Scout
- Unparalleled Data Quality
- Higher Quality Content
- 60% Fewer Hallucinations
Browse by: Latest US Patents, China's latest patents, Technical Efficacy Thesaurus, Application Domain, Technology Topic, Popular Technical Reports.
© 2025 PatSnap. All rights reserved.Legal|Privacy policy|Modern Slavery Act Transparency Statement|Sitemap|About US| Contact US: help@patsnap.com