Safe robot palletizer controlling method based on three-dimensional image reconstruction
A palletizing robot and three-dimensional reconstruction technology, applied in the field of robot control, can solve problems such as not taking into account robots and high hardware costs
- Summary
- Abstract
- Description
- Claims
- Application Information
AI Technical Summary
Problems solved by technology
Method used
Image
Examples
Embodiment Construction
[0025] The embodiments of the present invention are described in detail below. This embodiment is implemented on the premise of the technical solution of the present invention, and detailed implementation methods and specific operating procedures are provided, but the protection scope of the present invention is not limited to the following implementation example.
[0026] refer to figure 2 , the routine of this embodiment includes: a somatosensory 3D binocular vision sensor module, a three-dimensional reconstruction module based on image processing, a safety detection module, and a palletizing robot control system module. Among them, the somatosensory 3D vision sensor module is used to collect 3D information of the entire working environment at the operation site of the palletizing robot and send the information back to the 3D reconstruction module based on image processing. The module reconstructs the robot in 3D according to the image information. And the three-dimensiona...
PUM
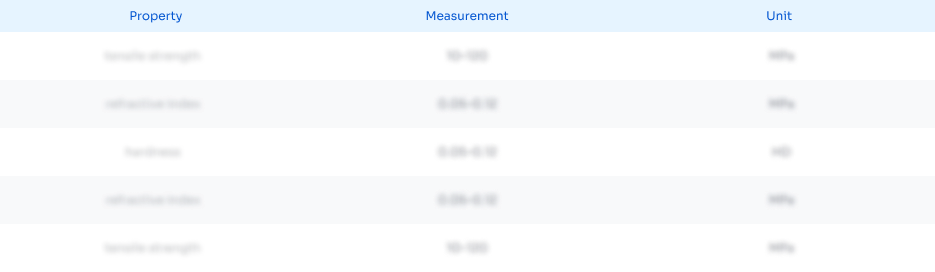
Abstract
Description
Claims
Application Information

- Generate Ideas
- Intellectual Property
- Life Sciences
- Materials
- Tech Scout
- Unparalleled Data Quality
- Higher Quality Content
- 60% Fewer Hallucinations
Browse by: Latest US Patents, China's latest patents, Technical Efficacy Thesaurus, Application Domain, Technology Topic, Popular Technical Reports.
© 2025 PatSnap. All rights reserved.Legal|Privacy policy|Modern Slavery Act Transparency Statement|Sitemap|About US| Contact US: help@patsnap.com