A machine oil cooler leakage detection method
An oil cooler, leak detection technology, applied in the direction of detecting the appearance of the fluid at the leak point, by measuring the acceleration and deceleration rate of the fluid, and using the liquid/vacuum degree for liquid tightness measurement, etc., which can solve the complicated operation and long cycle time. , oil cooler corrosion and other problems, to achieve the effect of simple and convenient operation, short measurement process rhythm, accurate leak detection and positioning
- Summary
- Abstract
- Description
- Claims
- Application Information
AI Technical Summary
Problems solved by technology
Method used
Examples
Embodiment 1
[0018] Leak testing for oil cooler model 1013000-81D includes the following steps:
[0019] 1), the interface is blocked and connected to the detection equipment:
[0020] Use process bolts to fix the oil cooler on the tray, and seal the full-flow machine filter port of the oil cooler; the outlet of the cooling medium of the oil cooler is connected, and the inlet of the cooling medium is connected to the inflatable device;
[0021] 2), leak detection and result judgment:
[0022] 2.1) Leakage rate detection: Inflate the oil cooler with air, the inflation pressure is 4bar, and the inflation time is 55 seconds; then wait for the pressure to balance, the balance time is 10s, and the measured pressure in the oil cooler after pressure balance is 3.9bar; Then, the leak rate of the oil cooler is detected by a leak detector. The detection time is 10 seconds, and the leak rate is 0.76cm 3 / min;
[0023] 2.2) Leak point detection: use the soap bubble method to detect the pressure reg...
Embodiment 2
[0027] Leak testing for oil cooler model 1013000-81D includes the following steps:
[0028] 1), the interface is blocked and connected to the detection equipment:
[0029] Use process bolts to fix the oil cooler on the tray, and seal the full-flow machine filter port of the oil cooler; the outlet of the cooling medium of the oil cooler is connected, and the inlet of the cooling medium is connected to the inflatable device;
[0030] 2), leak detection and result judgment:
[0031] 2.1) Leakage rate detection: Inflate the oil cooler with air, the inflation pressure is 4bar, and the inflation time is 55 seconds; then wait for the pressure to balance, the balance time is 10s, and the measured pressure in the oil cooler after pressure balance is 3.9bar; Then, the leakage rate of the oil cooler is detected by a leak detector. The detection time is 10 seconds, and the leakage rate is 15.6cm. 3 / min;
[0032] 2.2) Leak point detection: use the soap bubble method to detect the press...
Embodiment 3
[0036] Leak testing for oil cooler model 1013000-81D includes the following steps:
[0037] 1), the interface is blocked and connected to the detection equipment:
[0038] Use process bolts to fix the oil cooler on the tray, and seal the full-flow machine filter port of the oil cooler; the outlet of the cooling medium of the oil cooler is connected, and the inlet of the cooling medium is connected to the inflatable device;
[0039] 2), leak detection and result judgment:
[0040] 2.1) Leakage rate detection: Inflate the oil cooler with air, the inflation pressure is 4bar, and the inflation time is 55 seconds; then wait for the pressure to balance, the balance time is 10s, and the measured pressure in the oil cooler after pressure balance is 3.6bar; Then, the leakage rate of the oil cooler is detected by a leak detector. The detection time is 10 seconds, and the leakage rate is 106.6cm 3 / min;
[0041] 2.2) Leak point detection: use the soap bubble method to detect the press...
PUM
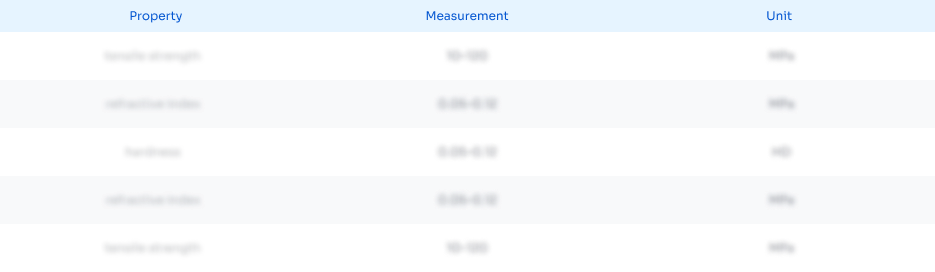
Abstract
Description
Claims
Application Information

- R&D
- Intellectual Property
- Life Sciences
- Materials
- Tech Scout
- Unparalleled Data Quality
- Higher Quality Content
- 60% Fewer Hallucinations
Browse by: Latest US Patents, China's latest patents, Technical Efficacy Thesaurus, Application Domain, Technology Topic, Popular Technical Reports.
© 2025 PatSnap. All rights reserved.Legal|Privacy policy|Modern Slavery Act Transparency Statement|Sitemap|About US| Contact US: help@patsnap.com