Dual-valve-element sealing structure
A technology with a sealed structure and double spools, applied in the direction of adding non-fuel substances to the fuel, internal combustion piston engines, engine components, etc., can solve the problems of substandard emissions, black smoke from the engine, power drop, etc., and solve the leakage exceeding the standard Effect
- Summary
- Abstract
- Description
- Claims
- Application Information
AI Technical Summary
Problems solved by technology
Method used
Image
Examples
Embodiment Construction
[0014] The present invention will be further described below in conjunction with the accompanying drawings.
[0015] Such as figure 2 As shown, a double-spool sealing structure includes a valve seat assembly 1 and a double-spool 2, and an annular groove 3 is dug on the bottom surface of the double-spool 2. The thickness of the double spool 2 is 6mm. The remaining wall thickness range of the double spool 2 digging the annular groove 3 is (1.5-3) mm. The thickness of the improved spool 2 is reduced from 7mm to 6mm from the 7mm of the pre-improved spool 2. At the same time, the bottom surface of the spool that is directly impacted by the exhaust gas adopts the method of digging a ring-shaped groove and thinning the solid body, so that the thinned part of the spool The remaining wall thickness is between (1.5-3) mm, which ensures that the valve core can undergo elastic deformation at high temperature.
PUM
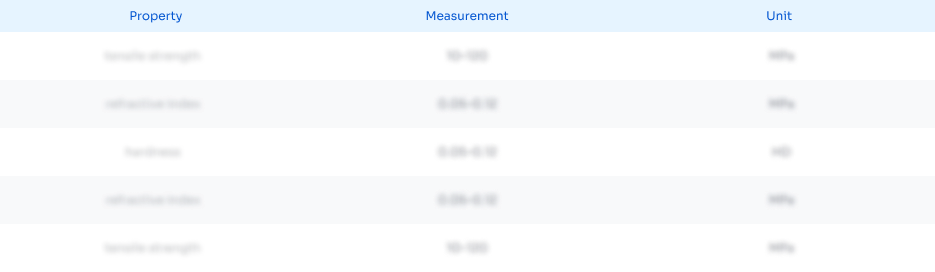
Abstract
Description
Claims
Application Information

- Generate Ideas
- Intellectual Property
- Life Sciences
- Materials
- Tech Scout
- Unparalleled Data Quality
- Higher Quality Content
- 60% Fewer Hallucinations
Browse by: Latest US Patents, China's latest patents, Technical Efficacy Thesaurus, Application Domain, Technology Topic, Popular Technical Reports.
© 2025 PatSnap. All rights reserved.Legal|Privacy policy|Modern Slavery Act Transparency Statement|Sitemap|About US| Contact US: help@patsnap.com