Rotary stamping compressed rotor plane cascade experimental system
- Summary
- Abstract
- Description
- Claims
- Application Information
AI Technical Summary
Problems solved by technology
Method used
Image
Examples
Embodiment Construction
[0029] The present invention is described in further detail below in conjunction with accompanying drawing:
[0030] Such as figure 1 As shown, the rotary stamping compression rotor planar cascade experimental system of the present invention is mainly composed of five parts: air source supply, wind tunnel shell, Laval nozzle 7, planar cascade experimental section 8, and experimental testing and data acquisition system. The motor 1 is controlled by the frequency conversion controller, and the centrifugal blower 2 is driven to provide a continuous air source, thereby obtaining a certain total pressure and speed of the air source. This part of the air flow passes through the pressure stabilization section 3 and enters the diffuser section 4 of the wind tunnel shell. The static pressure value in the circular to square diffuser section is improved, and after entering the square steady flow section 5, due to the vortex breaking and rectification effect of the built-in honeycomb and ...
PUM
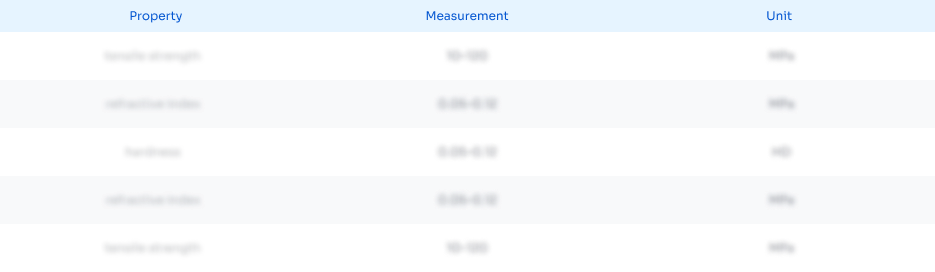
Abstract
Description
Claims
Application Information

- R&D
- Intellectual Property
- Life Sciences
- Materials
- Tech Scout
- Unparalleled Data Quality
- Higher Quality Content
- 60% Fewer Hallucinations
Browse by: Latest US Patents, China's latest patents, Technical Efficacy Thesaurus, Application Domain, Technology Topic, Popular Technical Reports.
© 2025 PatSnap. All rights reserved.Legal|Privacy policy|Modern Slavery Act Transparency Statement|Sitemap|About US| Contact US: help@patsnap.com